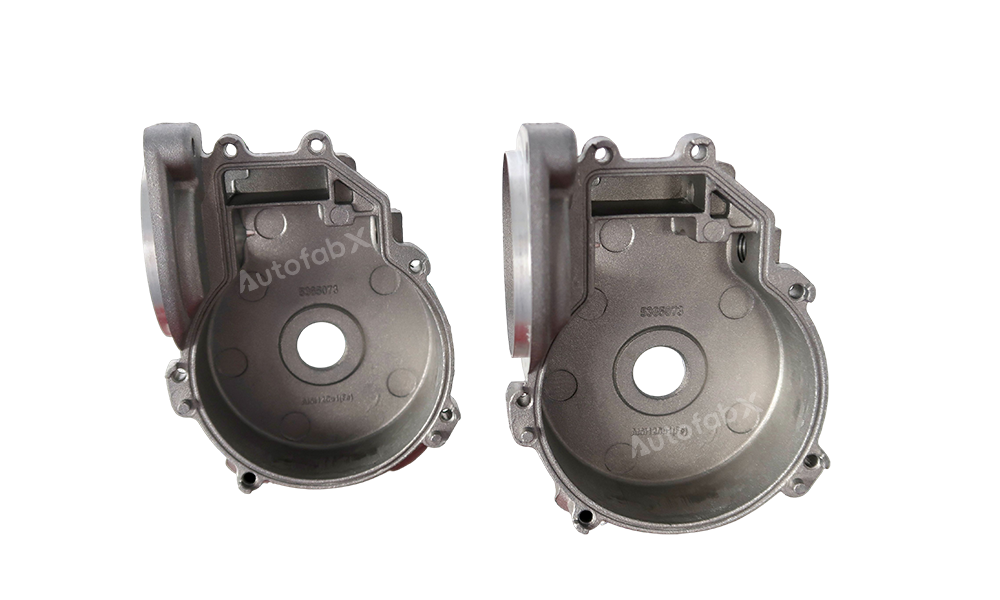
Quick Look
Density | Melting Point | Thermal Conductivity | Electrical Conductivity | Coefficient of Expansion |
---|---|---|---|---|
2.7 g/cm³ | 660°C | 205 W/m·K | 37.7 MS/m | 23.1 µm/m·K |
About the Material
ASTM | DIN | GB | Density (g/cm³) | Hardness | Tensile Strength,Yield (MPa) | Fatigue Strength (Mpa) | Elongation at Break (%) |
2017 | AlCuMg1 | 2A11&LY11 | 2.8 | 120~150 HB | 215~355 | 150~250 | 12~17 |
2024 | AlCuMg2 | 2A12&LY12 | 2.78 | 120~150 HB | 470~520 | 180~200 | 10~15 |
5052 | AlMg2.5 | 5A02&LF2 | 2.68 | 60 HB | 193 | 115 | 12 |
5083 | AlMg4.5Mn 3.3547 | 5083&LF4 | 2.68 | 60~75 HB | 310~420 | 130~190 | 12~18 |
6061 | AlMg1SiCu 3.3206 | 6061&LD30 | 2.7 | 60~95 HB | 240 | 100 | 12~17 |
6063 | AlMgSi0.5 | 6063&LD31 | 2.7 | 50~80 HB | 145 | 80 | 10~15 |
6082 | 3.2315 ① | 2.71 | 95~110 HB | 320~430 | 150~250 | 8~12 | |
7075 | AlZnMgCu1.5 | 7A09&LC9 | 2.8 | 150~180 HB | 505 | 200 | 11~13 |
Advantages:
Lightweight: Aluminum alloys are significantly lighter than other metals, making them suitable for aerospace and automotive applications.
High Machinability: Aluminum is easy to cut, drill, and mill, allowing for faster production with lower tooling costs.
Corrosion Resistant: Natural resistance to corrosion reduces the need for additional coatings in many environments.
Thermal Conductivity: Ideal for components requiring heat dissipation, such as heat sinks.
Limitations:
Strength Limitations: Aluminum alloys may not provide the same level of strength as steel or titanium in high-load applications.
Surface Softness: Aluminum is softer compared to other metals, making it susceptible to scratches and dents.
Cost: Depending on the alloy and application, aluminum can be more expensive compared to other materials like carbon steel.
Chemical Composition Table for Aluminum Alloys
Element | Typical Percentage (%) |
Aluminum (Al) | 85-99 |
Magnesium (Mg) | 0.5-6 |
Silicon (Si) | 0.5-12 |
Copper (Cu) | 0.1-5 |
Zinc (Zn) | 0.1-6 |
Mechanical Machining Properties Table for Aluminum Alloys
Property | Value |
Machinability Rating | Excellent |
Cutting Speed (m/min) | 200-300 |
Tool Wear Resistance | Moderate |
Coolant Requirement | Optional |
Surface Finish Quality | High |
Design Parameters Table for CNC Machining Aluminum Alloys
Maximum Bulid Size (mm) | Minimum Wall Thickness (mm) | Minimum Assembly Gap (mm) | Tolerance (mm) | Minimum End Mill Size (mm) | Minimum Drill Size (mm) |
3600x2500x600 | 1 | 0.01 | Minimum 0.01 | 1 | 0.5 |
Industry Applications and Case Studies for CNC Machining Aluminum Alloys
Aerospace Industry:
Application: Production of lightweight structural components, brackets, and fittings.
Case Study: An aerospace company used CNC machining to create aluminum alloy brackets, reducing the weight of the aircraft and improving fuel efficiency.
Automotive Industry:
Application: Manufacturing of engine parts, heat exchangers, and transmission components.
Case Study: An automotive manufacturer utilized CNC machining to produce aluminum cylinder heads, achieving excellent thermal management and reduced overall vehicle weight.
Electronics Industry:
Application: Production of heat sinks, casings, and electronic enclosures.
Case Study: A consumer electronics company used CNC machining to manufacture aluminum heat sinks, providing efficient thermal management for electronic devices.
Frequently Asked Questions (FAQs) about CNC Machining Aluminum Alloys
What are the benefits of using aluminum alloys in CNC machining?
Aluminum alloys are lightweight, corrosion-resistant, and highly machinable, making them ideal for various applications.
Is CNC machining suitable for high-volume aluminum alloy production?
Yes, CNC machining is effective for both prototyping and large-scale production, with consistent quality and precision.
What industries benefit from CNC machining aluminum alloys?
Industries such as aerospace, automotive, electronics, and consumer goods benefit from aluminum's lightweight, strength, and machinability.
How does aluminum compare to steel in terms of cost and performance?
Aluminum is generally more expensive than carbon steel but offers better machinability, corrosion resistance, and weight savings.
What are the limitations of using aluminum alloys in CNC machining?
Limitations include lower strength compared to steel and susceptibility to surface scratches and dents.
Can aluminum alloys be anodized after CNC machining?
Yes, anodizing is a common post-processing step for aluminum alloys to enhance corrosion resistance and surface hardness.
What tolerances can be achieved with CNC machining aluminum alloys?
Typical tolerances are ±0.1 mm, depending on the specific requirements of the part.
Finishing Options
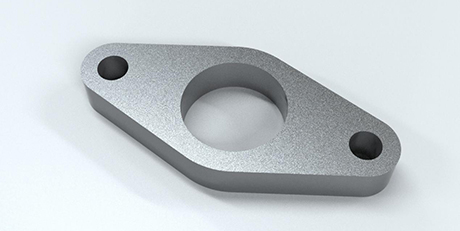
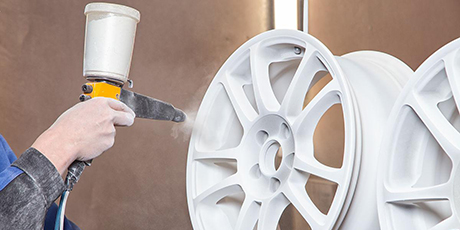
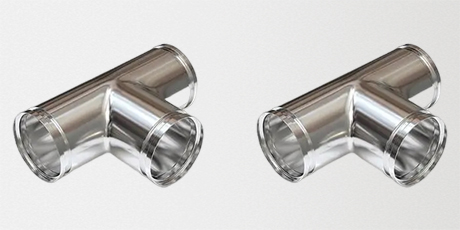
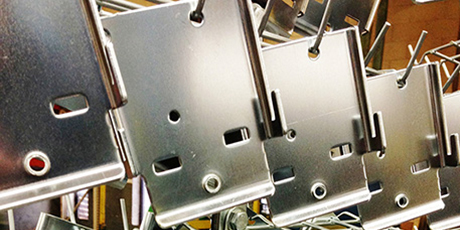
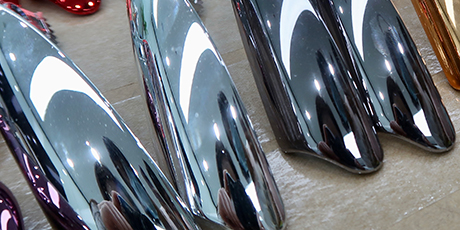
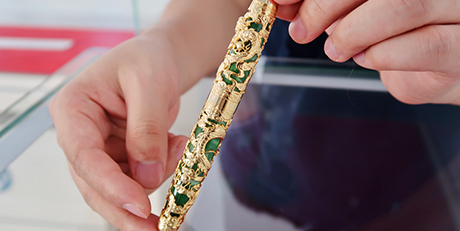
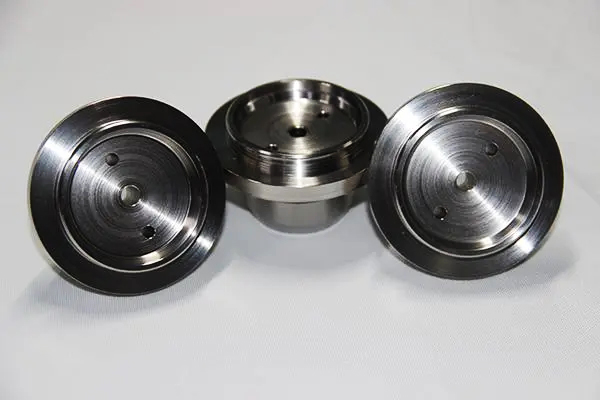
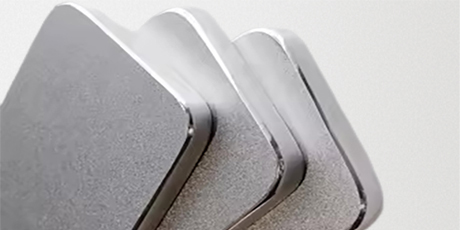
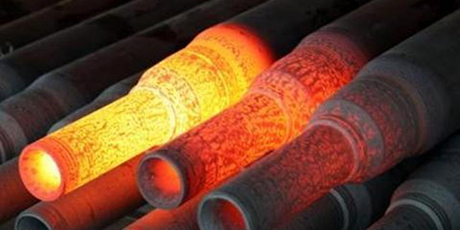
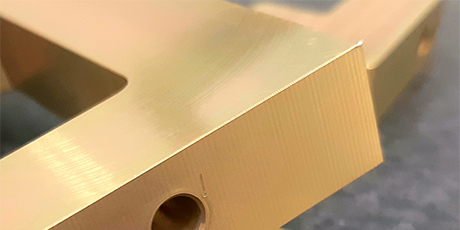
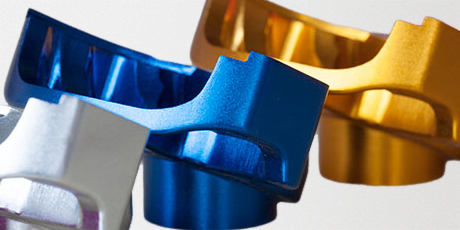
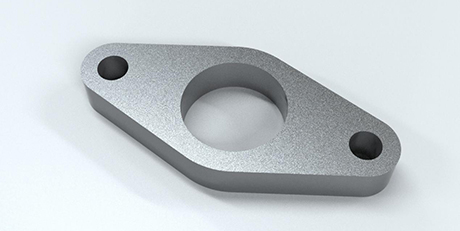
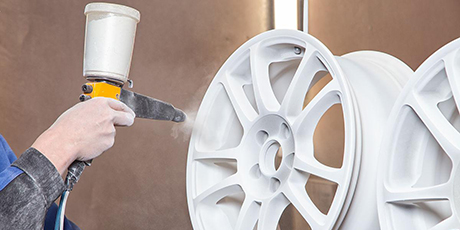
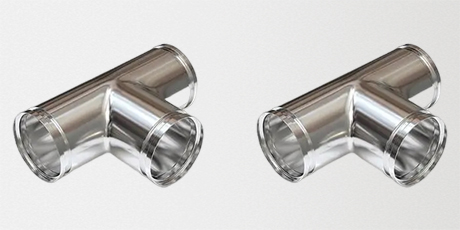
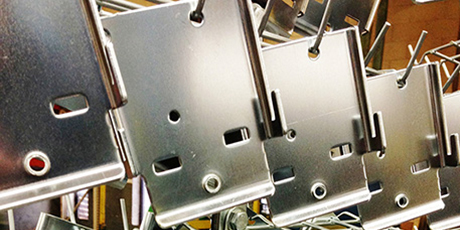
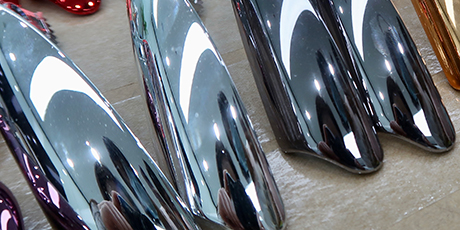
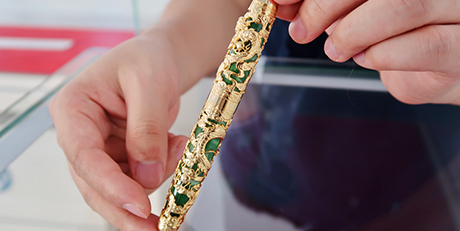
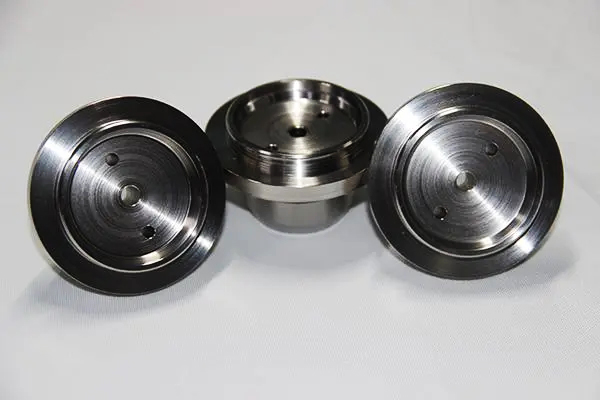
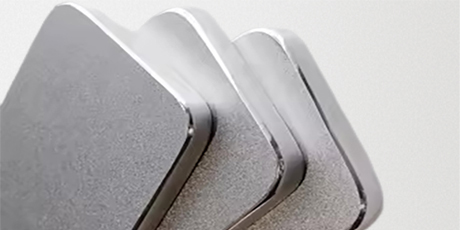
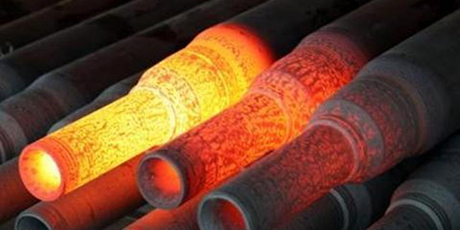
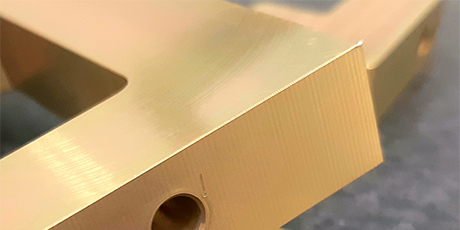
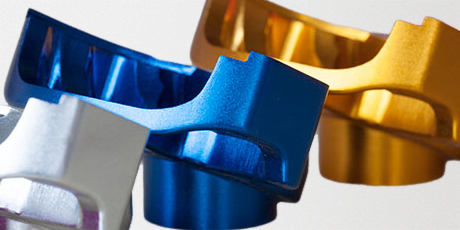
Parts Made by AutofabX
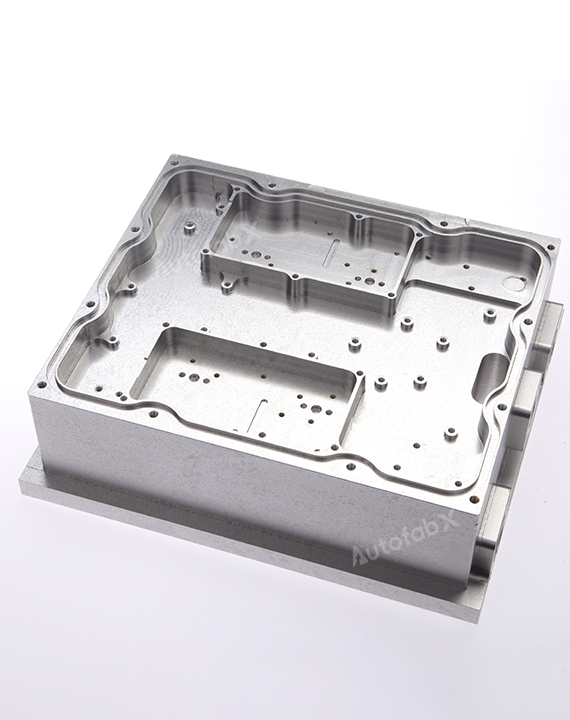
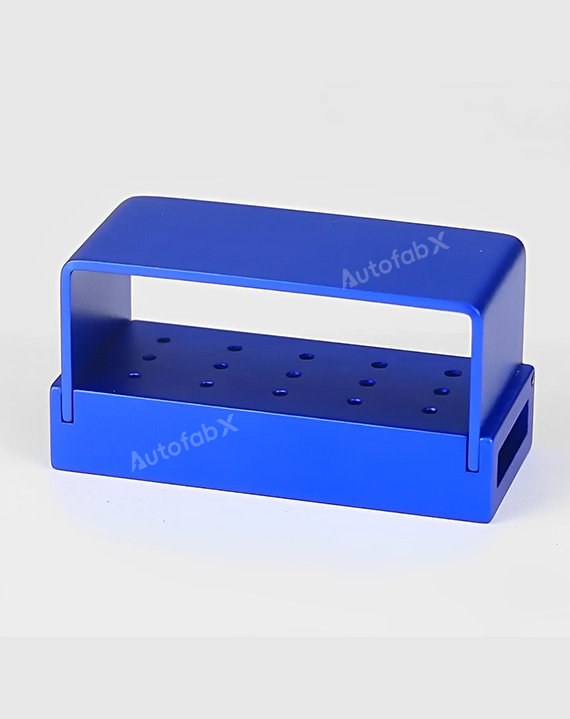
