Custom Online Metal Injection Molding(MIM) Services
Personalized Support, Exclusive First-Order Discount, Faster Lead Times with AutofabX
Start A New Quote
STEP | STP | IGS | DWG | DXF | PDF FilesMetal Injection Molding(MIM) Materials
MIM Iron Base Alloys
High Strength and Durability, Complex Geometries, Cost Efficiency for High Volumes
Finishing:
Sand Blasting, Polishing, Powder Coating, Painting, Electrocoating, Shot Blasting, Galvanizing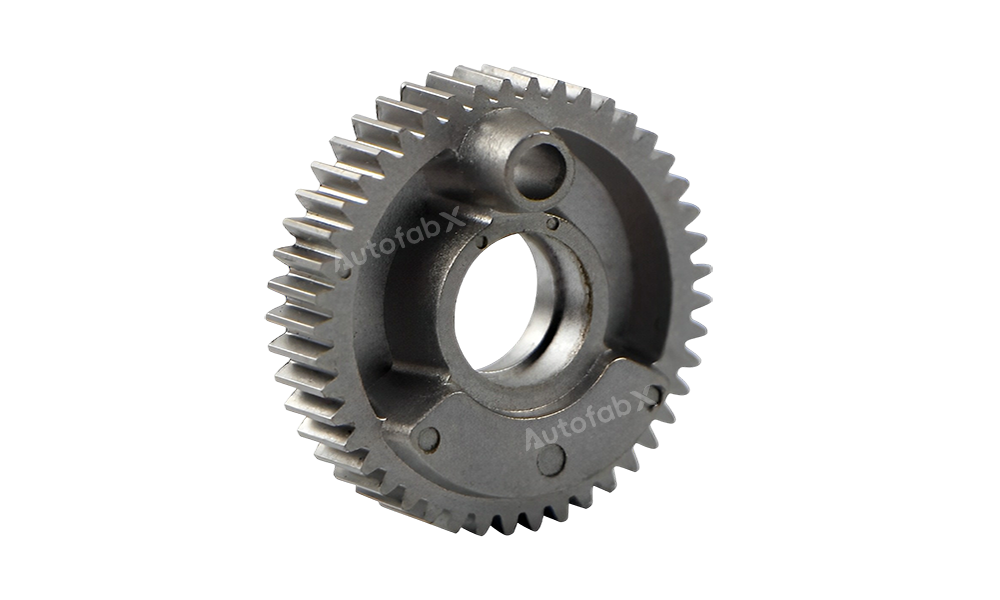
Overview
Metal Injection Molding(MIM) is a manufacturing process that combines the design flexibility of plastic injection molding with the material strength of powder metallurgy. It is used to produce complex, high-strength metal parts in large volumes with precision and efficiency.
AutofabX Platform Advantages in MIM:
Quick Delivery: AutofabX leverages advanced production scheduling and automated systems to ensure rapid lead times, helping clients meet tight deadlines and reduce time to market.
Stable Quality: With rigorous quality control standards and precision engineering, AutofabX ensures consistent part quality, minimizing defects and guaranteeing high-performance MIM components.
Cost-Effective Solutions: By optimizing manufacturing processes and minimizing waste, AutofabX offers competitive pricing without compromising on quality, making it an attractive choice for cost-conscious clients.
These key benefits—quick delivery, stable quality, and cost-effectiveness—make AutofabX a leading platform for clients seeking reliable and efficient MIM solutions.
Process
Metal Injection Molding (MIM) Process Steps:
Mixing: Metal powder is mixed with a binder to create a homogeneous feedstock.
Granulation: The mixture is granulated to produce feedstock suitable for injection molding.
Injection Molding: The feedstock is injected into a mold using an injection molding machine, producing a "green body."
Debinding (Cleaning): The molded green body undergoes debinding to remove the binder.
Sintering: The debound green body is sintered at high temperatures to fuse the metal powder particles, forming the final metal component.
This process combines the advantages of powder metallurgy and the flexibility of plastic injection molding to efficiently produce complex metal parts.
Equipment and Leading Brands in MIM:
Mixing and Granulation Equipment:
Leading Brands: Eirich, MTI Mischtechnik, Hosokawa Alpine
Injection Molding Machines:
Leading Brands: ARBURG, ENGEL, Sumitomo (SHI) Demag
Debinding Furnaces:
Leading Brands: Cremer, Elnik Systems, ECM Technologies
Sintering Furnaces:
Leading Brands: Seco/Warwick, Ipsen, Nabertherm
These top-tier brands provide the high-quality equipment required to maintain precision, efficiency, and consistency throughout the MIM process.
Analyze
Advantages:
Complex Geometries: MIM allows for the production of intricate and complex geometries that are difficult to achieve with traditional manufacturing methods.
Material Properties: The final products retain the desirable mechanical properties of metal, such as strength and hardness.
High Volume Production: MIM is suitable for mass production, allowing for the efficient production of large quantities of parts.
Minimal Material Waste: The process minimizes material waste, making it a cost-effective and environmentally friendly option.
Limitations:
High Initial Costs: The tooling and setup costs for MIM can be high, making it less suitable for small production runs.
Size Limitations: MIM is generally limited to small and medium-sized parts due to the constraints of the injection molding process.
Binder Removal: The debinding process can be time-consuming and requires careful control to ensure part quality.
Limited Material Options: While many metals can be used in MIM, the selection is still more limited compared to other metalworking techniques.
Applications
Industries and Applications of MIM:
Automotive Industry:
Applications: Production of complex automotive components, such as gears, turbocharger parts, and sensor housings.
Case Study: A leading automotive manufacturer used MIM to produce high-precision gears, reducing production time and material costs while maintaining component durability.
Medical and Dental Industry:
Applications: Manufacturing of surgical instruments, orthodontic brackets, and implantable devices.
Case Study: A medical device company utilized MIM to produce minimally invasive surgical tools, achieving high precision and biocompatibility.
Consumer Electronics:
Applications: Fabrication of small and intricate components like connectors, hinges, and structural parts for electronic devices.
Case Study: An electronics brand employed MIM to manufacture durable smartphone components, allowing for a sleek design without compromising strength.
Aerospace Industry:
Applications: Production of lightweight and complex parts used in aircraft systems and components.
Case Study: An aerospace supplier used MIM to create high-strength components for aircraft engines, enhancing fuel efficiency and reducing weight.
Firearms and Defense:
Applications: Manufacturing of components such as trigger guards, hammers, and other intricate firearm parts.
Case Study: A firearms manufacturer used MIM to produce high-quality, precision parts, improving consistency and reducing overall production costs.
These applications showcase the versatility of MIM across various industries, making it an ideal solution for producing complex, high-performance metal parts.
Quality Control
Quality Control Standards and Inspection Methods in MIM:
Dimensional Inspection:
Tools: Coordinate Measuring Machines (CMM), optical comparators, and calipers are used to verify dimensional accuracy against specifications.
Density and Porosity Testing:
Methods: Archimedes' principle is often used to measure part density, ensuring the sintered components meet required density levels. X-ray tomography can be used to assess internal porosity.
Mechanical Property Testing:
Tests: Tensile testing, hardness testing, and impact testing are performed to ensure the final parts meet mechanical strength requirements.
Surface Finish Inspection:
Techniques: Surface profilometers are used to check surface roughness, ensuring parts meet required aesthetic and functional criteria.
Visual and Microscopic Examination:
Inspection: Visual inspection and microscopic examination are carried out to identify surface defects, cracks, or other inconsistencies.
Non-Destructive Testing (NDT):
Methods: Techniques such as X-ray and ultrasonic testing are used to inspect internal defects without damaging the parts.
These quality control standards and inspection methods help ensure that MIM components meet the stringent requirements of various industries, maintaining consistency, reliability, and performance.
FAQs
Frequently Asked Questions (FAQs) about MIM:
What types of materials can be used in MIM?
MIM can use a variety of metals, including stainless steel, titanium, nickel, copper, and alloys. However, the selection is somewhat limited compared to other metalworking methods.
What are the typical part sizes for MIM?
MIM is generally best suited for small and medium-sized parts, typically weighing less than 100 grams, though larger parts can be made under certain conditions.
What industries benefit most from MIM?
Industries such as automotive, medical, consumer electronics, aerospace, and firearms benefit significantly from MIM due to its ability to produce complex, high-strength parts efficiently.
What are the cost factors in MIM?
The cost factors include tooling, material, and production volume. While the initial tooling cost can be high, MIM becomes cost-effective for large-scale production runs.
How does MIM compare to traditional machining?
MIM is more efficient for producing complex geometries and high volumes, while traditional machining is often preferred for low-volume or simpler parts. MIM also reduces material waste compared to machining.
What are the main limitations of the MIM process?
Limitations include high initial tooling costs, size constraints, the need for careful binder removal, and a somewhat limited selection of materials.
How is quality ensured in MIM?
Quality is ensured through various inspection methods, including dimensional inspection, density testing, mechanical property testing, and non-destructive testing to ensure parts meet industry standards.
What are the lead times for MIM production?
Lead times can vary depending on the complexity of the part and the volume of production, but typically range from several weeks to a few months, including tooling and production setup.
Can MIM produce parts with complex internal structures?
Yes, MIM is well-suited for producing parts with complex internal geometries that would be challenging or impossible to create using traditional manufacturing techniques.
Is MIM environmentally friendly?
Yes, MIM is considered environmentally friendly due to minimal material waste and the efficient use of raw materials.
Parts Made by AutofabX
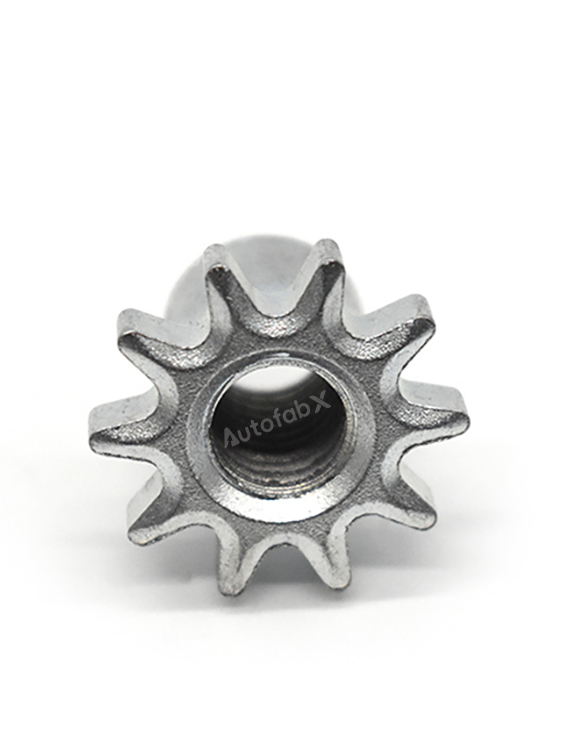
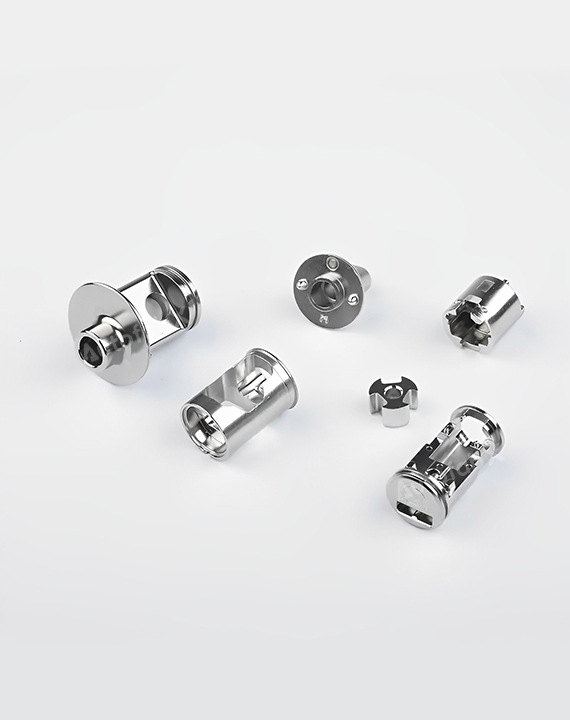

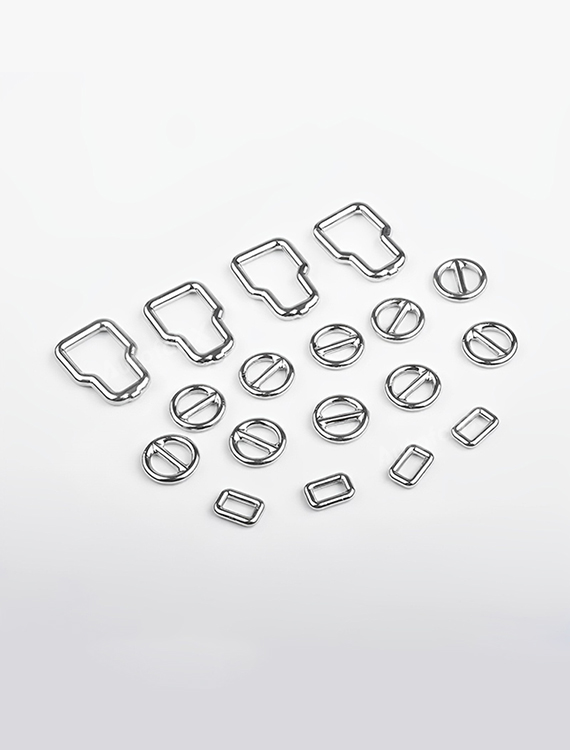
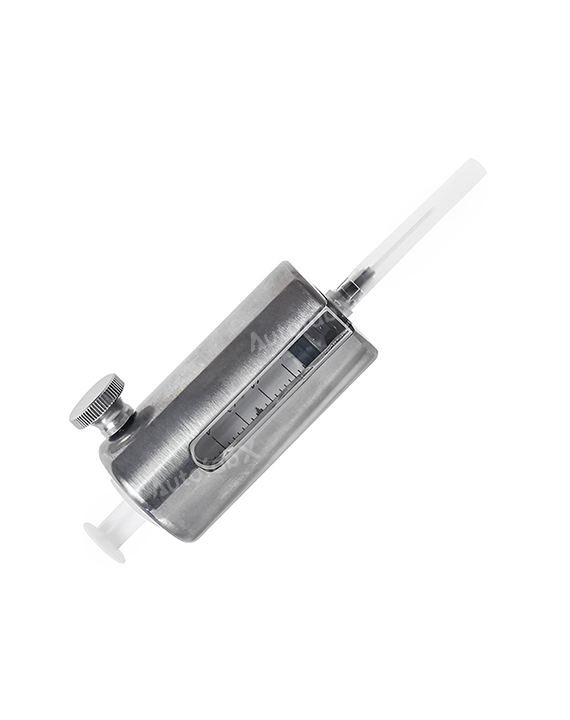
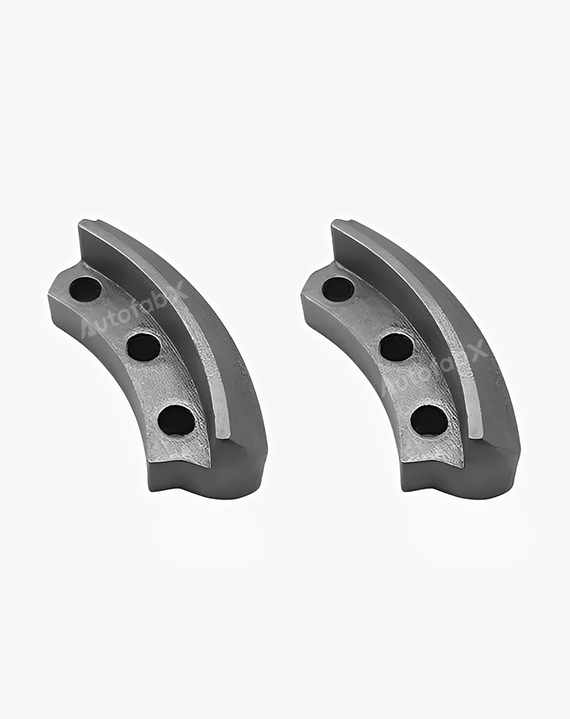
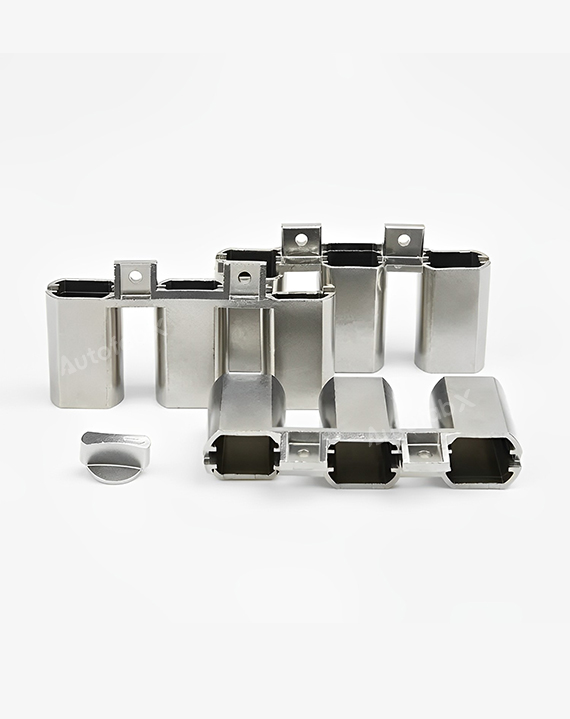