Custom Online Urethane and Silicone Casting Services
Suitable for manufacturing prototypes and parts ranging from 100 to 1000 pieces. Maximum build size of 1500*1000mm. ISO 9001:2015, ISO 13485 and AS9100D certified.
Start A New Quote
STEP | STP | IGS | DWG | DXF | PDF FilesUrethane and Silicone Casting Materials
Nylon-Like
High Strength and Toughness, High-Temperature Resistance, Good Dimensional Stability
Finishing:
Matte/Frosted, High-Gloss, Semi-Gloss, Textured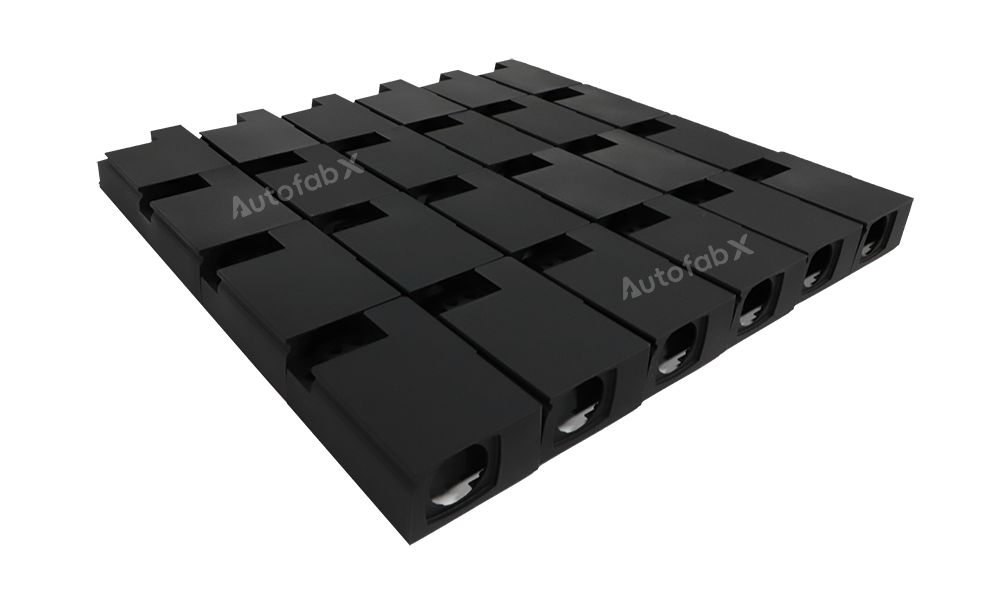
Overview
Urethane Casting(also known as Silicone Molding or Urethane Casting) is a manufacturing process used to create high-quality, low-volume plastic parts. This method involves making a silicone mold from a master pattern (typically created through 3D printing or CNC machining) and then using the mold to produce multiple copies of the original part. It is widely used for prototyping, bridge production, or small runs of end-use parts. Urethane Casting is often favored for its ability to reproduce complex geometries and fine details while using a variety of materials with different physical properties.
AutofabX Platform Advantages in Urethane Casting:
AutofabX is an emerging U.S.-based platform specializing in urethane casting with several distinct advantages:
Professional Technical Support: AutofabX has a team of dedicated experts providing in-depth technical support throughout the casting process, ensuring clients receive high-quality results.
Quick Turnaround: The platform is designed to provide rapid prototyping and production services, significantly reducing lead times.
Quality Assurance: AutofabX guarantees stringent quality control, providing reliable parts that meet client expectations.
Competitive Pricing: With optimized processes and cost efficiencies, AutofabX offers prices that are highly competitive compared to other local and international suppliers.
Vast Supplier Network: The platform boasts a large network of vetted suppliers, ensuring access to the right capabilities and resources for any project requirement.
Customized Solutions: AutofabX offers tailored solutions based on specific customer needs, including material selection, surface finish options, and design optimization.
Sustainable Practices: AutofabX emphasizes sustainability by minimizing waste during the casting process and promoting the use of environmentally friendly materials.
Process
Steps Involved in Urethane Casting:
Master Model Creation: Create a master model using 3D printing or CNC machining.
Mold Making: Pour liquid silicone around the master model to create a mold. The mold is cured and then cut open to remove the master model.
Casting: Polyurethane resin is mixed, degassed, and poured into the silicone mold. The mold is then cured, often in a vacuum or pressure chamber.
Demolding and Finishing: Once cured, the part is removed from the mold and any necessary finishing touches, such as trimming or painting, are applied.
Equipment and Leading Brands for Urethane Casting:
Vacuum Chambers: Used for degassing silicone and resin to ensure parts are free of air bubbles. Leading brands include VACUUBRAND and BVV, with prices ranging from $1,000 to $5,000.
Mixing Equipment: For accurate resin mixing, brands like Thinky offer specialized mixing machines that start around $5,000.
Pressure Pots: To prevent bubbles in the final product, pressure pots (e.g., CA Technologies models) are used, costing between $500 and $3,000.
Ovens for Curing: Used to accelerate the curing process, ovens from brands like Blue M range from $3,000 to $10,000 depending on size and features.
Analyze
Advantages of Urethane Casting:
Fast Production: Urethane casting is a relatively quick process, ideal for producing functional prototypes or small production runs.
Cost-Effective: Compared to injection molding, urethane casting requires lower upfront costs since expensive metal tooling isn’t needed.
Versatility: A wide range of materials with different properties can be cast, including flexible, rigid, or transparent options.
Surface Finish: Parts produced through urethane casting can achieve excellent surface quality and detailed finishes, which can be further enhanced with post-processing.
Scalable Production: Urethane casting allows for easy scalability, from single prototypes to small batch production runs, making it flexible for evolving project needs.
Color Customization: Urethane parts can be easily color-matched or tinted, providing customization options for branding or aesthetic purposes.
Limitations of Urethane Casting:
Limited Volume: Urethane casting is most suitable for low-volume production (usually fewer than 100 parts), as silicone molds wear out after repeated use.
Material Limitations: While versatile, the material options are not as broad as with traditional injection molding, and urethane materials may not have the same long-term durability.
Tolerances: Tolerances may not be as precise as those achievable with CNC machining or injection molding, which can limit the process for highly precise applications.
Industries and Applications of Urethane Casting:
Automotive Prototypes:
Urethane casting is often used for car interior components during prototype development. Compared to CNC machining, urethane casting offers greater flexibility in material properties, making it ideal for testing.
Case Study - Automotive Prototypes: A U.S.-based automotive startup needed low-volume interior components to test ergonomic designs. Using AutofabX's urethane casting services, they received cost-effective, durable parts with excellent surface finishes in just 10 days. Compared to traditional CNC machining, they saved 30% on costs and reduced lead time by 40%.
Consumer Electronics Enclosures:
This process is used to create enclosures for early-stage consumer electronics prototypes, offering cost savings over injection molding during the initial phases.
Case Study - Consumer Electronics Prototype: A consumer electronics firm used urethane casting to create a small batch of enclosures for a wearable device. The parts were made in under two weeks and had a production-quality finish, allowing the company to perform market testing before committing to injection molding. This approach saved them 50% in initial production costs.
Medical Devices:
Urethane casting is suitable for producing ergonomic and durable casings for medical devices. Compared to 3D printing, the parts have a more production-like finish, crucial for usability testing.
Case Study - Medical Device Housing: A medical device company used AutofabX to create housing for handheld diagnostic tools. The urethane casting process provided production-quality parts that allowed for ergonomic testing and regulatory approvals before mass production. Compared to 3D printing, the urethane cast parts had superior finish quality and were more representative of the final product.
Aerospace Components:
Aerospace companies use urethane casting to produce lightweight, functional prototypes for cabin interiors. The flexibility to use fire-retardant materials and the high-quality finish makes urethane casting a preferred choice.
Industrial Machinery Components:
Urethane casting is used for creating covers, housings, and other functional parts for industrial machinery. Compared to traditional fabrication, it offers significant time and cost savings during the prototyping phase.
Quality Control Standards and Inspection Methods in Urethane Casting:
Standards: Dimensional tolerances are typically within ±0.5% for urethane cast parts, and the visual quality is inspected to meet customer specifications.
Testing Tools and Methods:
Calipers and Micrometers: For dimensional inspection.
Hardness Testers: Used to verify the hardness of the cast parts.
Vacuum Testing: Ensures there are no air bubbles that could weaken the part.
Handling Quality Issues: Defects such as air bubbles or poor surface quality are mitigated through improved mold preparation, proper mixing, and degassing of the urethane resin.
Design Guidelines for Urethane Casting
Maximum Part Size: Typically up to 1500 mm depending on the mold.
Tolerance: Dimensional tolerances are generally around ±0.15 mm.
Minimum Order Quantity: Urethane casting is well-suited for quantities of 5 to 25 parts.
Minimum Wall Thickness: Recommended minimum wall thickness is 1.5 mm for structural integrity.
Post-Processing Options: Painting, texturing, and inserting are common post-processing options.
Lead Time: From master pattern to final parts, the lead time is typically 7-14 days depending on complexity.
Frequently Asked Questions (FAQs) about Urethane Casting:
What types of materials can be used for urethane casting?A variety of polyurethane resins are available, including rigid, flexible, and transparent options, allowing a wide range of properties.
How durable are urethane cast parts?Urethane parts are suitable for functional testing and end-use in low-volume applications. However, they may not match the durability of parts made from high-performance thermoplastics.
How many parts can be made from one silicone mold?Typically, a silicone mold can produce between 15 and 25 parts before it starts to degrade.
Can urethane cast parts be painted?Yes, parts can be painted and finished to match desired aesthetics, making them ideal for visual models or marketing samples.
What are the typical lead times for urethane casting?Lead times are usually 1-2 weeks, depending on the complexity of the part and the production volume.
Is urethane casting suitable for functional testing?Yes, urethane cast parts are often used for functional testing due to their ability to mimic production materials closely.
Can urethane casting be used for clear parts?Yes, clear polyurethane resins can be used to create transparent parts, often used for lenses or enclosures that need visibility.
What is the cost difference between urethane casting and injection molding?Urethane casting has lower initial costs due to the absence of expensive tooling, making it ideal for low-volume production, while injection molding becomes more cost-effective for larger production volumes.
How do I ensure the best surface finish in urethane casting?The surface finish quality depends on the master model's finish. Using a high-quality master and proper mold care will help achieve the best results.
What are common defects in urethane casting and how are they prevented?Common defects include air bubbles and warping. These can be prevented by proper degassing, using pressure curing, and ensuring correct mixing ratios of the resin.
Parts Made by AutofabX
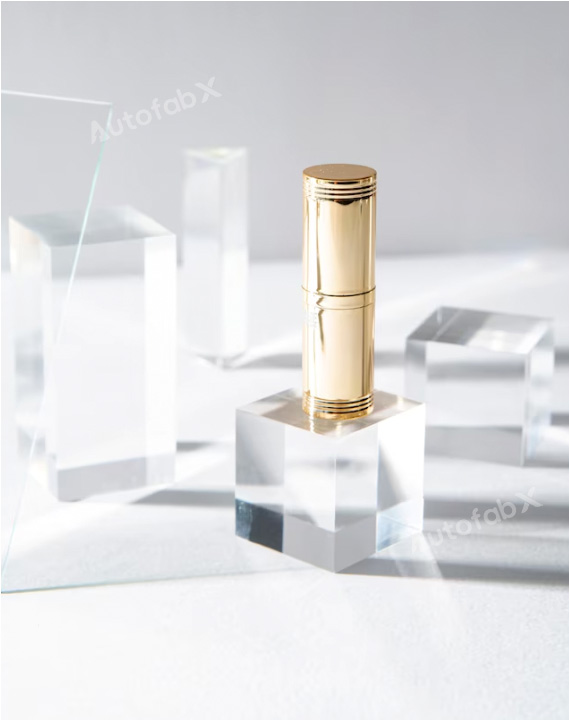
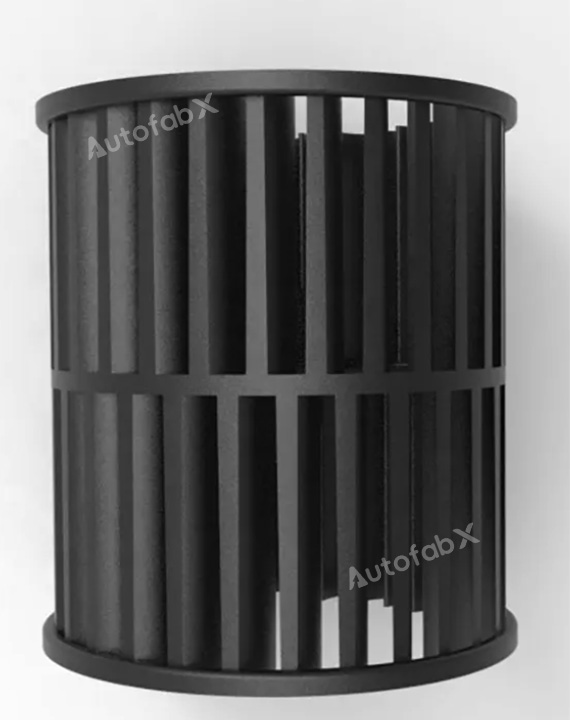
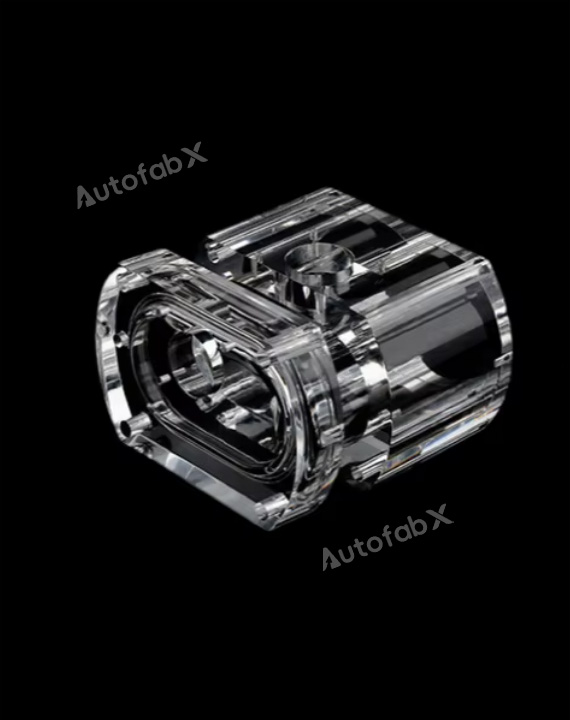
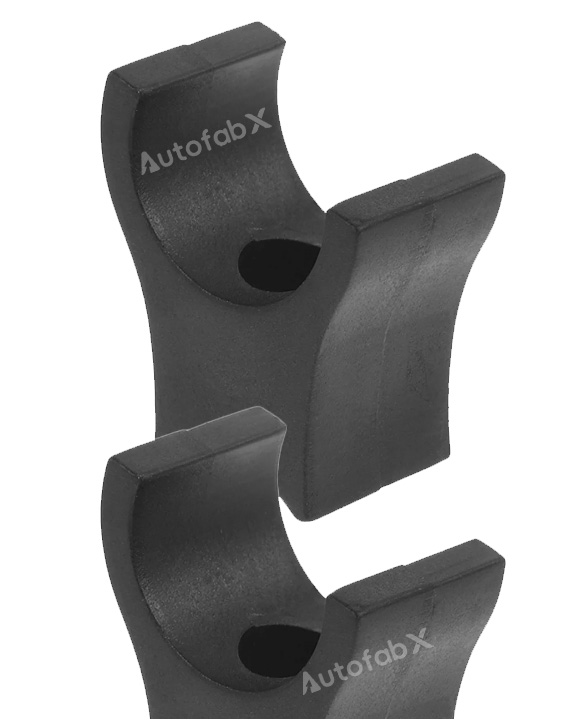
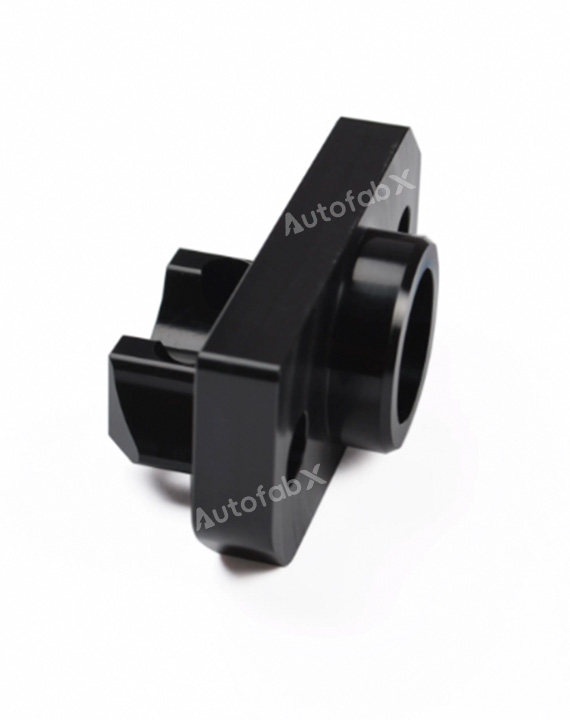
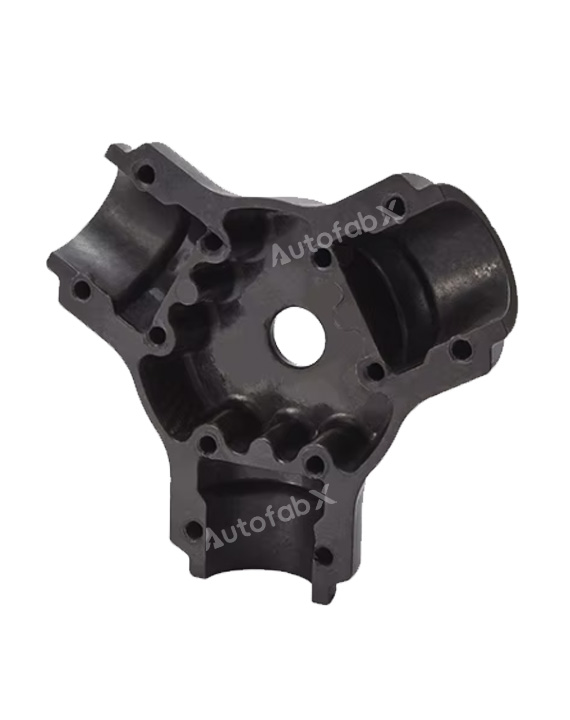
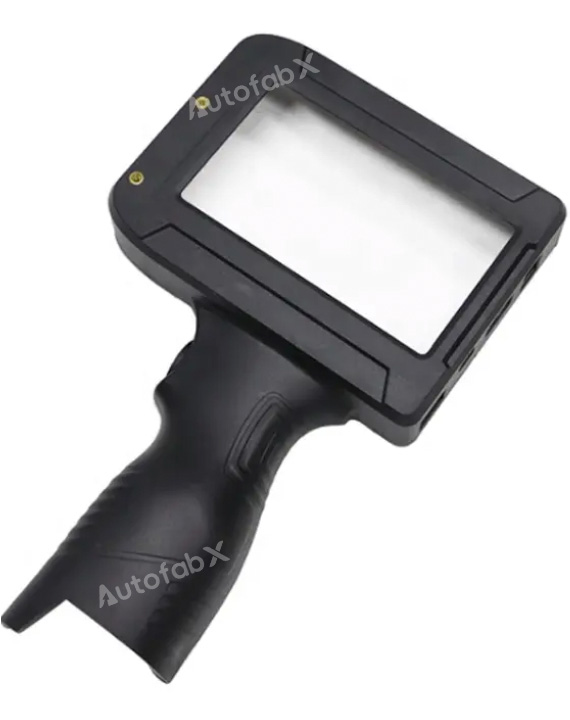
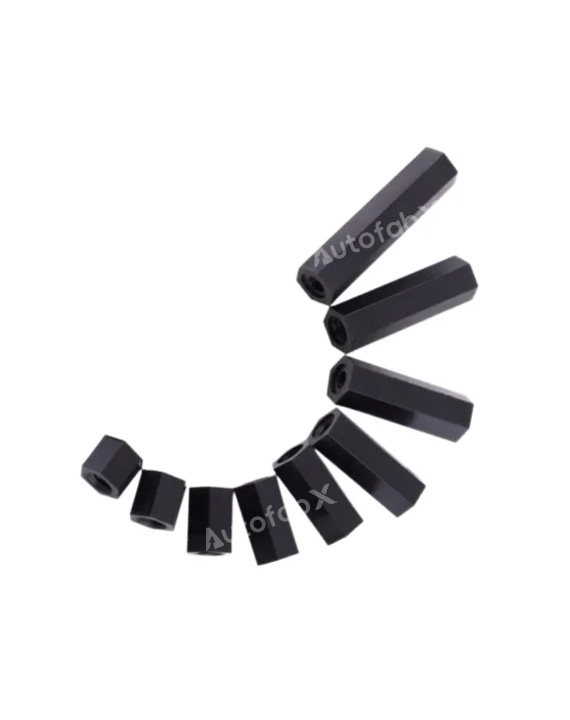
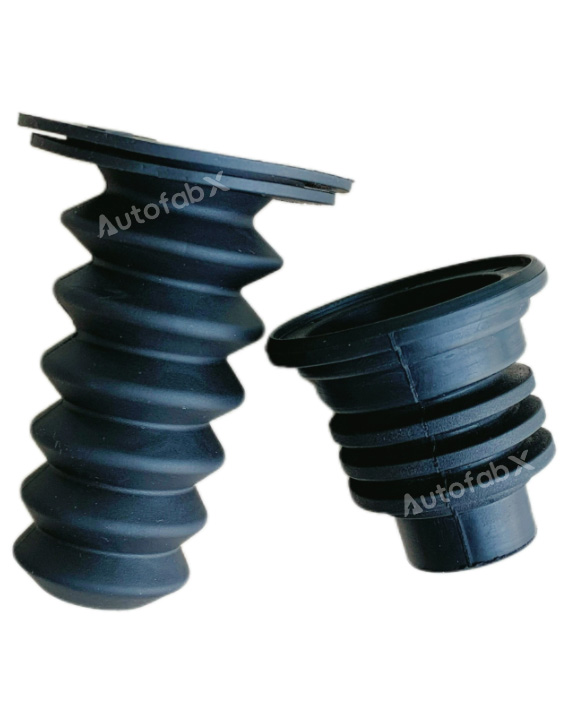