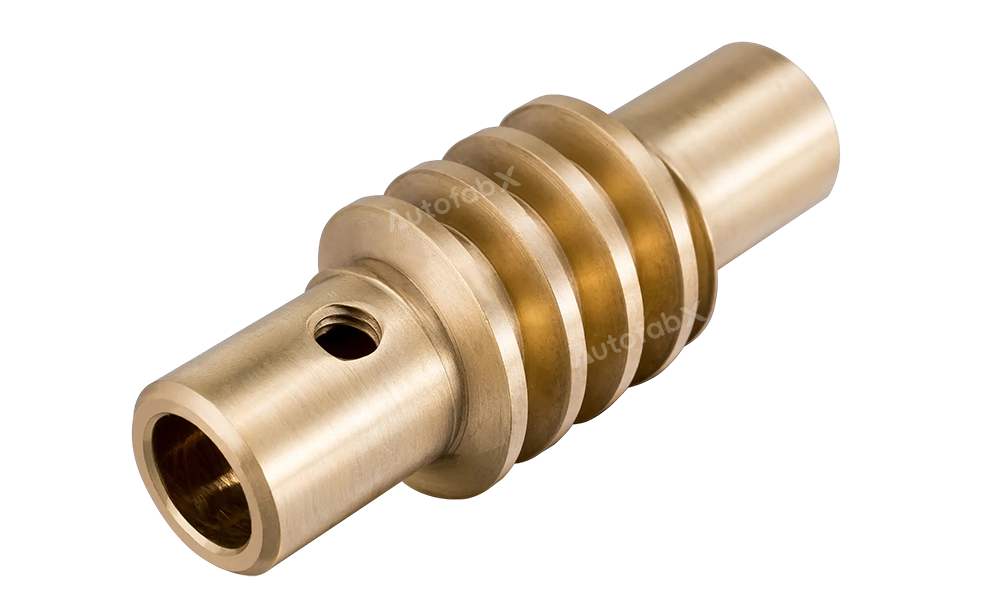
Quick Look
Density | Melting Point | Thermal Conductivity | Electrical Conductivity | Coefficient of Expansion |
---|---|---|---|---|
8.7-8.9 g/cm³ | 950-1050°C | 50-60 W/m·K | 10-15 MS/m | 16-18 µm/m·K |
About the Material
ASTM | DIN | GB | Density (g/cm³) | Hardness | Tensile Strength,Yield (MPa) | Fatigue Strength (Mpa) | Elongation at Break (%) |
C521 | CuSn8 | QSn7-0.2 | 8.9 | 90~120 HB | 450~600 | 150~250 | 10~15 |
C172 | CuBe2&2.1247 | QBe2 | 8.8 | 180~220 HB | 700~900 | 250~400 | 4~10 |
C182 | CuCr | QCr0.5 | 8.9 | 150~210 HB | 700~800 | 200~350 | 8~12 |
Advantages:
Wear Resistance: Excellent resistance to wear, making bronze ideal for components that experience high friction.
Corrosion Resistance: Natural resistance to corrosion, especially in salty or wet environments, such as marine applications.
Good Machinability: Bronze alloys are easy to machine, offering high precision and reducing production time.
Attractive Finish: The material has an appealing natural finish, ideal for decorative purposes.
Limitations:
Material Cost: Bronze can be more expensive compared to other metals like aluminum or steel.
Density: Bronze is heavier than many other metals, which may limit its use in weight-sensitive applications.
Softness: Bronze is softer compared to other alloys, making it susceptible to dents and deformation under heavy loads.
Chemical Composition Table for Bronze Alloys
Element | Typical Percentage (%) |
Copper (Cu) | 80-90 |
Tin (Sn) | 5-12 |
Zinc (Zn) | 1-5 |
Lead (Pb) | ≤ 1.5 |
Nickel (Ni) | ≤ 1.0 |
Mechanical Machining Properties Table for Bronze Alloys
Property | Value |
Machinability Rating | Good |
Cutting Speed (m/min) | 100-150 |
Tool Wear Resistance | Moderate |
Coolant Requirement | Optional |
Surface Finish Quality | High |
Design Parameters Table for CNC Machining Bronze Alloys
Maximum Bulid Size (mm) | Minimum Wall Thickness (mm) | Minimum Assembly Gap (mm) | Tolerance (mm) | Minimum End Mill Size (mm) | Minimum Drill Size (mm) |
850x500x500 | 1 | 0.01 | Minimum 0.01 | 1 | 0.5 |
Industry Applications and Case Studies for CNC Machining Bronze Alloys
Marine Industry:
Application: Production of propellers, valves, and fittings.
Case Study: A marine equipment manufacturer used CNC machining to create bronze propeller blades, ensuring durability and resistance to saltwater corrosion.
Automotive Industry:
Application: Manufacturing of bushings, bearings, and gears.
Case Study: An automotive parts supplier utilized CNC machining to produce bronze bearings, reducing friction and wear in high-performance engines.
Decorative and Architectural:
Application: Production of statues, plaques, and architectural fittings.
Case Study: An architectural firm used CNC machining to create intricate bronze fittings, adding an aesthetic touch to building exteriors.
Frequently Asked Questions (FAQs) about CNC Machining Bronze Alloys
What are the benefits of using bronze alloys in CNC machining?
Bronze alloys offer high wear resistance, good machinability, and excellent corrosion resistance, making them suitable for various applications.
Is CNC machining suitable for high-volume bronze alloy production?
Yes, CNC machining is effective for both prototyping and high-volume production, with consistent quality.
What industries benefit from CNC machining bronze alloys?
Industries such as marine, automotive, and architectural benefit from bronze's wear resistance, corrosion resistance, and aesthetic qualities.
How does bronze compare to brass in terms of machinability?
Bronze is generally harder and offers better wear resistance than brass, but both are relatively easy to machine.
What are the limitations of using bronze alloys in CNC machining?
Limitations include higher material costs, weight, and susceptibility to deformation under heavy loads.
Can bronze alloys be coated to improve surface hardness?
Yes, bronze alloys can be coated or treated to improve hardness and wear resistance.
What tolerances can be achieved with CNC machining bronze alloys?
Typical tolerances are ±0.1 mm, depending on the specific requirements of the part.
Finishing Options
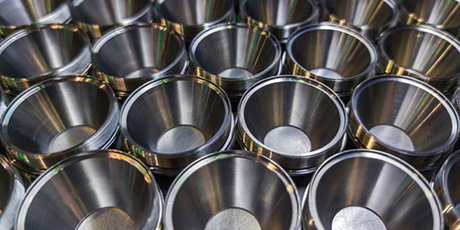
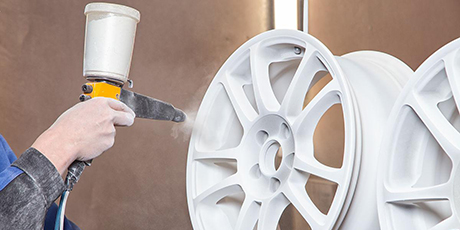
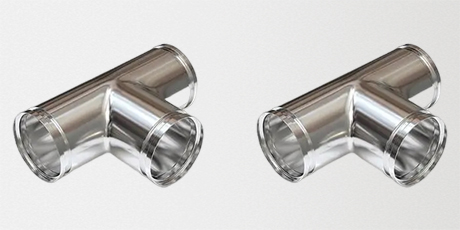
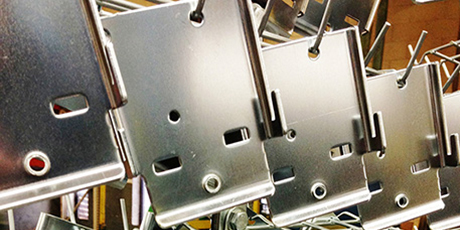
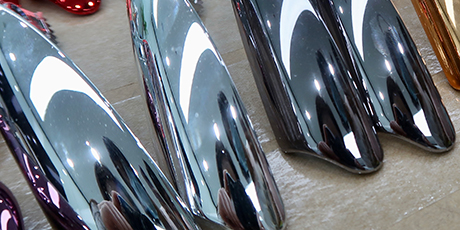
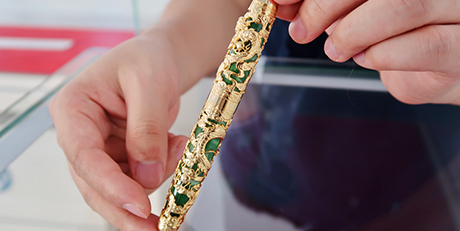
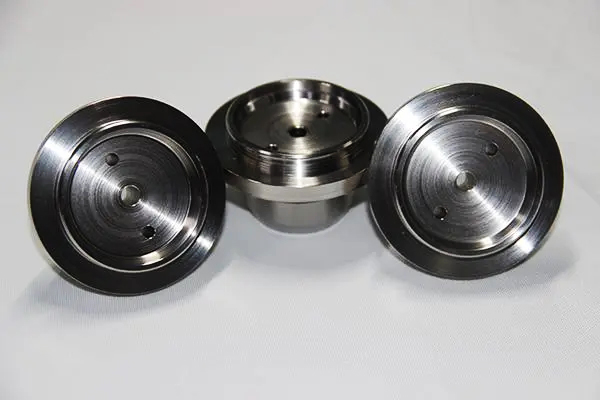
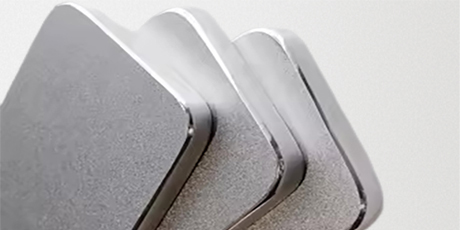
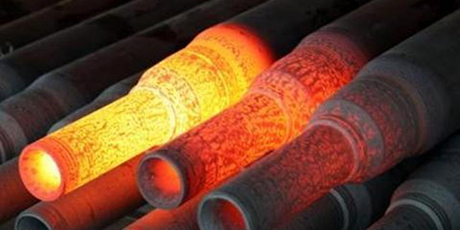
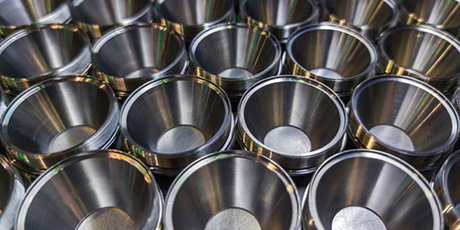
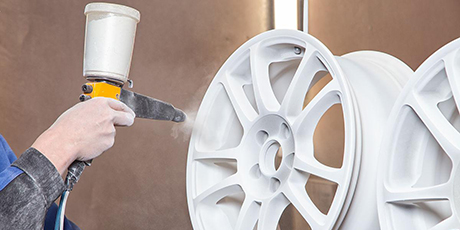
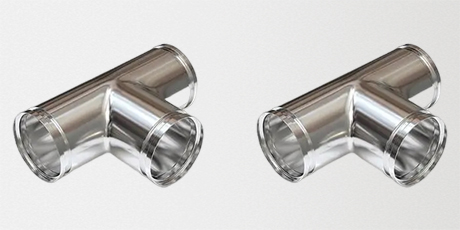
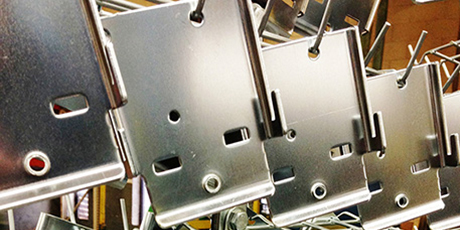
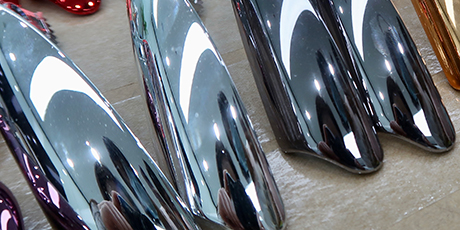
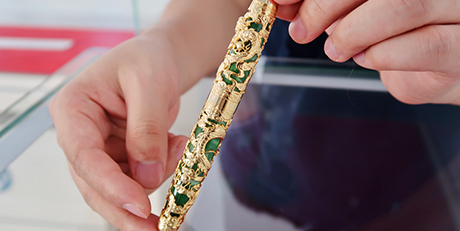
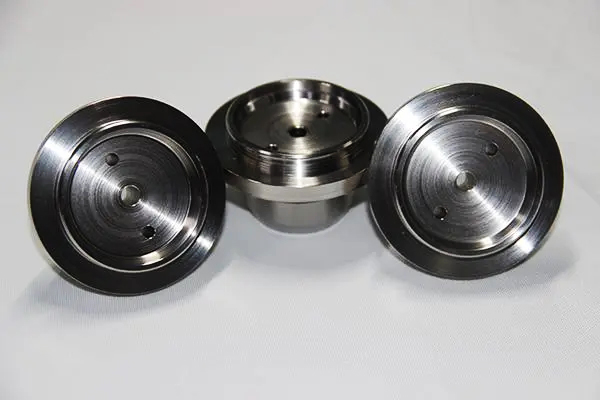
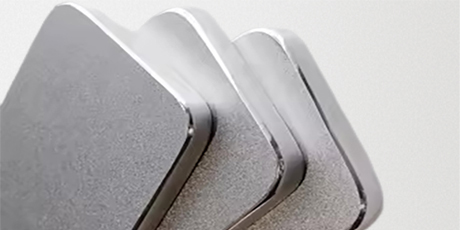
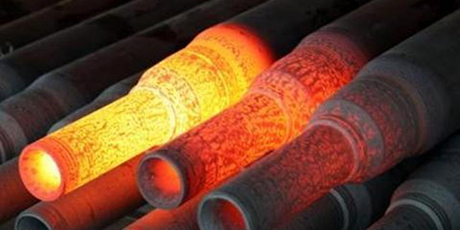
Parts Made by AutofabX

