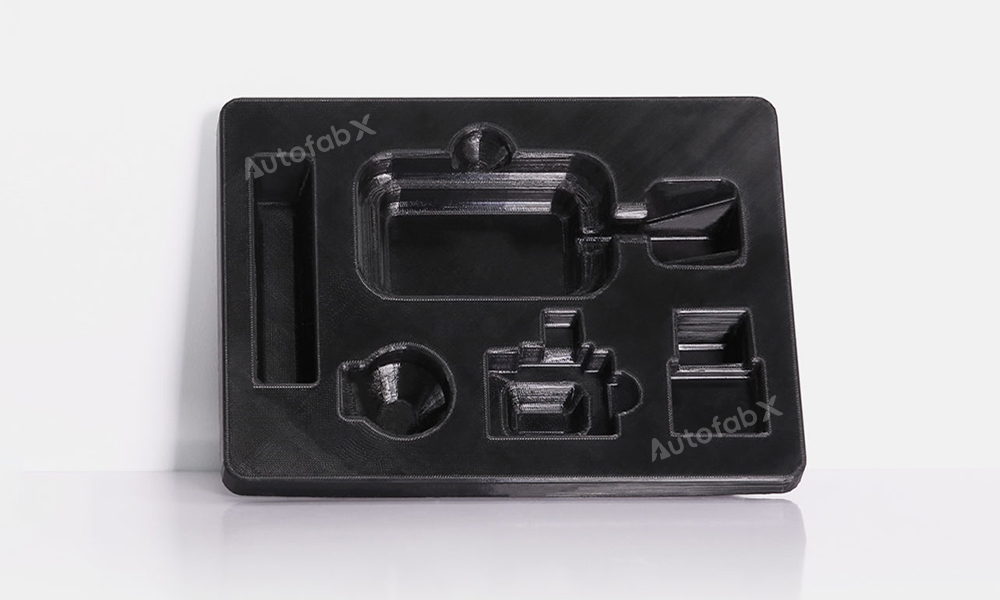
Quick Look
Density(g/cm³) | Tensile Strength | Young's Modulus | Elongation at Break | Glass Transition Temperature |
---|---|---|---|---|
1.3 | 32MPa | 1523 ± 50 (MPa) | 4.40% | 79℃ |
About the Material
Advantages:
High Strength and Durability: PETG offers high impact resistance and durability, making it suitable for functional parts.
Chemical Resistance: PETG is resistant to many chemicals, making it suitable for applications in chemically harsh environments.
Low Warping: PETG has low shrinkage, reducing the risk of warping during printing and ensuring good dimensional accuracy.
Ease of Use: PETG is easier to print compared to ABS, with good layer adhesion and minimal warping.
Limitations:
Stringing: PETG is prone to stringing during printing, which may require fine-tuning of printing parameters.
Lower Heat Resistance: PETG has a lower heat resistance compared to ABS, limiting its use in high-temperature environments.
Surface Finish: PETG parts may have a glossy surface finish, which might not be suitable for all applications and may require post-processing.
Chemical Composition Table for PETG
Component | Composition |
Polyethylene Terephthalate Glycol | 100% |
Additives (Colorants) | Varies |
Mechanical Machining Properties Table for PETG
Property | Value |
Machinability Rating | Moderate |
Cutting Speed (m/min) | 15-25 |
Tool Wear Resistance | Moderate |
Coolant Requirement | Optional |
Surface Finish Quality | High |
Design Parameters Table for FDM Printing with PETG
Maximum Bulid Size(mm) | Minimum Wall Thickness | Minimum Drill Size | Minimum Assembly Gap | Tolerance |
250*250*250 | 0.6mm | 1mm | 0.2mm | ±0.3% (lower limit of ±0.1 mm) |
Industry Applications and Case Studies for FDM Printing with PETG
Consumer Goods:
Application: Production of durable household items and prototypes.
Case Study: A home goods company used PETG to prototype a kitchen utensil, leveraging its durability and food-safe properties.
Industrial Applications:
Application: Manufacturing of custom machine components and jigs.
Case Study: An industrial equipment manufacturer used PETG to produce custom jigs and fixtures for their assembly line, benefiting from PETG's chemical resistance and strength.
Medical Industry:
Application: Production of medical device housings and components.
Case Study: A medical device company used PETG to create housings for electronic medical equipment, ensuring good impact resistance and chemical durability.
Frequently Asked Questions (FAQs) about FDM Printing with PETG
What are the benefits of using PETG in 3D printing?
PETG combines strength, chemical resistance, and ease of printing, making it suitable for functional prototypes and end-use parts.
Is PETG suitable for functional parts?
Yes, PETG is ideal for functional parts that require impact resistance and durability, but it may not be suitable for high-temperature applications.
What industries benefit from FDM printing with PETG?
Industries such as consumer goods, industrial manufacturing, and medical benefit from the strength, chemical resistance, and food-safe properties of PETG.
How accurate is FDM printing with PETG?
FDM printing with PETG can achieve tolerances of ±0.5 mm, which is suitable for most prototyping and functional applications.
What post-processing is required for PETG-printed parts?
Post-processing may include sanding, painting, or annealing to improve the surface finish and strength.
Can PETG be used for food-contact applications?
PETG is often considered food-safe, but it is important to ensure that the specific filament used is certified for food contact.
How strong are PETG-printed parts?
PETG-printed parts are strong and durable, with good impact resistance, making them suitable for functional applications.
Finishing Options
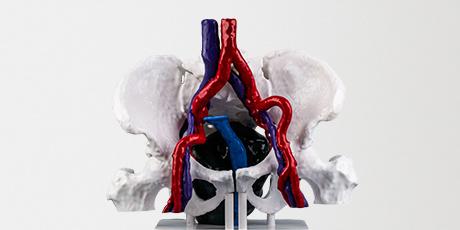
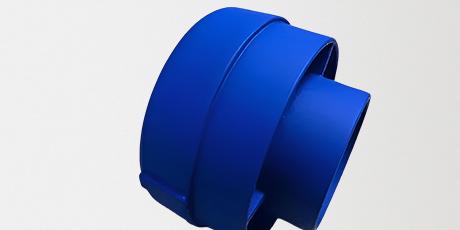
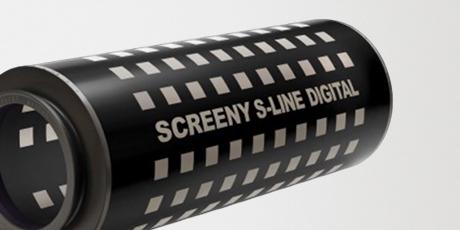
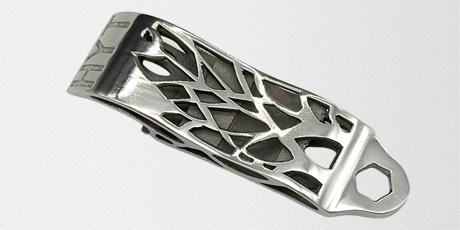
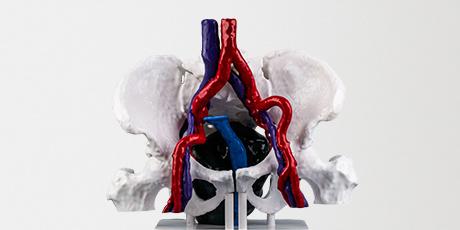
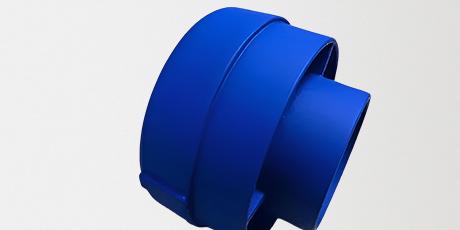
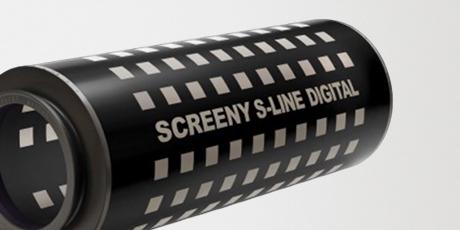
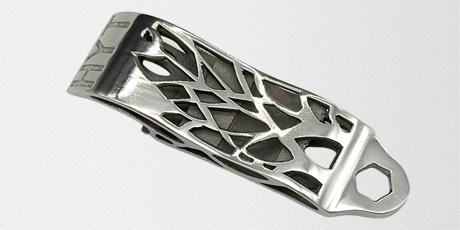
Parts Made by AutofabX
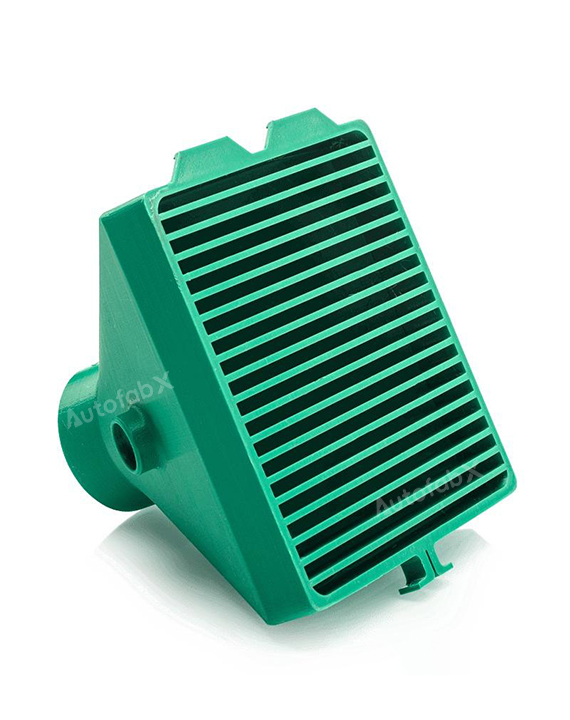
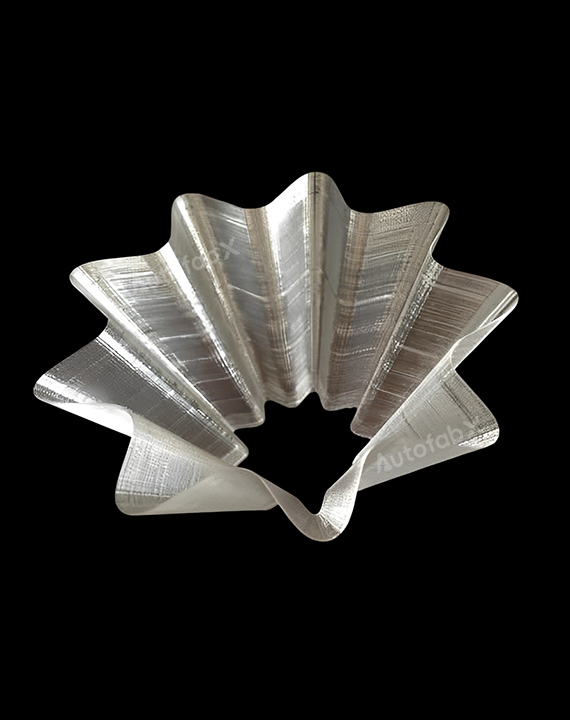