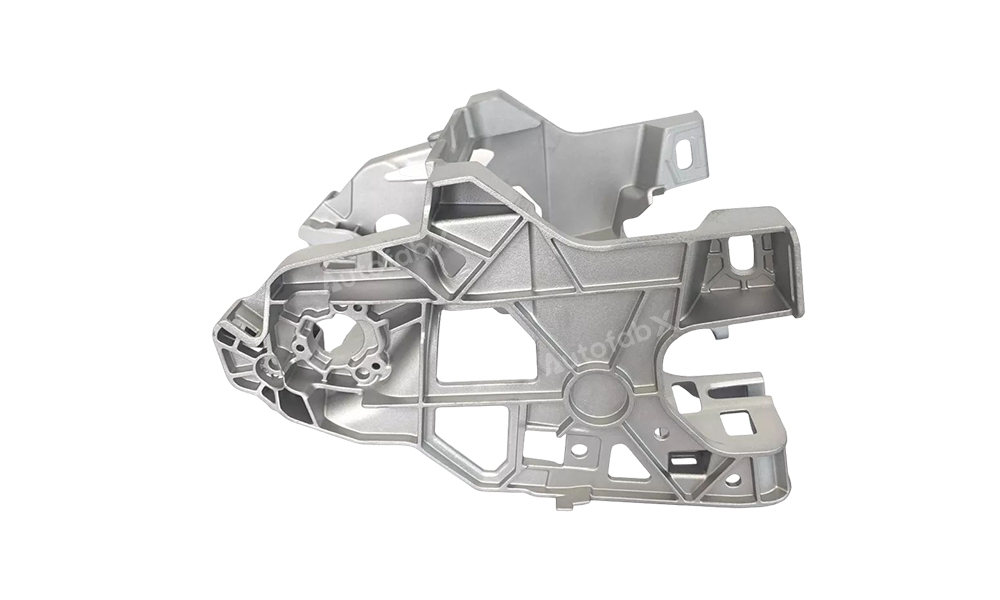
Quick Look
Density | Melting Point | Thermal Conductivity | Electrical Conductivity | Coefficient of Expansion |
---|---|---|---|---|
2.7 g/cm³ | 660.3°C | 205 W/m·K | 37.7 MS/m | 23.1 µm/m·K |
About the Material
Advantages:
Lightweight: Aluminum alloys are significantly lighter than other metals, making them suitable for applications where weight reduction is critical.
Corrosion Resistance: Aluminum alloys provide good resistance to corrosion, reducing the need for additional coatings or treatments.
Complex Geometries: The MIM process allows for intricate geometries that are challenging to achieve through traditional casting, enabling more design flexibility.
High Thermal Conductivity: Aluminum alloys are ideal for applications requiring efficient heat dissipation.
Cost-Effective for Prototyping and Low Volume: The process is efficient for small-batch production and prototyping, making it suitable for custom applications.
Limitations:
Lower Strength Compared to Steel: While aluminum alloys are strong, they do not match the strength of steel, which may limit their use in high-load applications.
High Thermal Expansion: Aluminum has a higher coefficient of thermal expansion, which can be a limitation in applications requiring tight dimensional stability under varying temperatures.
Porosity Issues: The casting process can sometimes result in porosity, which may need additional processing to ensure the integrity of the part.
Cost for High Volumes: For very large-scale production, other methods such as die casting may be more cost-effective than Rapid Investment Casting.
Chemical Properties Table
Element | Aluminum (Al) | Silicon (Si) | Magnesium (Mg) | Copper (Cu) | Zinc (Zn) | Iron (Fe) |
Typical Percentage (%) | 85-95 | 5-12 | 0.1-1.0 | 0.1-4.0 | 0.1-0.5 | ≤ 0.7 |
Machining Properties Table
Machinability Rating | Cutting Speed (m/min) | Tool Wear Resistance | Coolant Requirement | Surface Finish Quality |
Excellent | 200-600 | Moderate | Recommended | High |
Rapid Investment Casting Aluminum Alloys Design Parameters
Maximum Bulid Size (mm) | Minimum Wall Thickness (mm) | Minimum Assembly Gap (mm) | Tolerance | Minimum End Mill Size (mm) | Minimum Drill Size (mm) |
600x600x600 | 1 | 0.1 | 0.30% | / | / |
Industry Applications and Case Studies for Rapid Investment Casting Aluminum Alloys:
Automotive Industry:
Application: Production of lightweight structural parts, engine components, and brackets.
Case Study: An automotive manufacturer used Rapid Investment Casting to produce complex aluminum brackets, achieving a significant weight reduction and improving fuel efficiency.
Aerospace Industry:
Application: Manufacturing of components like airframe parts and brackets.
Case Study: An aerospace company used aluminum alloys to create lightweight yet strong airframe components, reducing overall aircraft weight and enhancing performance.
Electronics Industry:
Application: Production of heat sinks and electronic housings.
Case Study: A leading electronics manufacturer utilized Rapid Investment Casting for aluminum heat sinks, resulting in efficient heat dissipation for high-performance electronics.
Consumer Products:
Application: Production of intricate and lightweight parts for sports equipment and household items.
Case Study: A consumer goods company used Rapid Investment Casting to create lightweight aluminum bicycle components, resulting in improved performance and rider comfort.
Frequently Asked Questions (FAQs) about Rapid Investment Casting Aluminum Alloys:
What are the benefits of using aluminum alloys in Rapid Investment Casting?
Aluminum alloys offer a combination of lightweight, corrosion resistance, excellent machinability, and thermal conductivity, making them ideal for a range of applications.
Is Rapid Investment Casting suitable for high-volume aluminum alloy production?
While it is most cost-effective for prototyping and low-volume production, for high-volume production, methods like die casting may be more economical.
What industries benefit from aluminum alloys in Rapid Investment Casting?
Industries such as automotive, aerospace, electronics, and consumer products benefit greatly from the use of aluminum alloys due to their lightweight and high thermal conductivity.
How does aluminum alloy casting compare to other metals in terms of cost?
Aluminum is generally more cost-effective than titanium or stainless steel, especially for parts that do not require extreme strength.
What are the limitations of using aluminum alloys in Rapid Investment Casting?
Limitations include lower strength compared to steel, high thermal expansion, and the potential for porosity, which may require additional inspection and processing.
What are the typical applications for aluminum alloys in Rapid Investment Casting?
Typical applications include automotive brackets, aerospace airframe components, electronic heat sinks, and consumer product components.
How can porosity in aluminum alloy castings be minimized?
Proper control of the casting process, including degassing and using quality molds, can help reduce porosity in aluminum castings.
Are aluminum alloys corrosion-resistant in all environments?
Aluminum alloys are naturally corrosion-resistant but may require additional coatings or anodizing in highly corrosive environments, such as marine applications.
Finishing Options
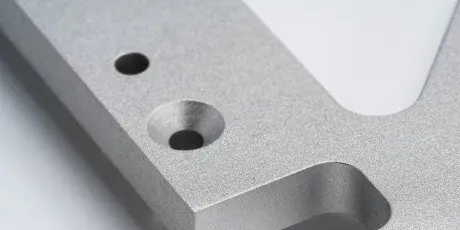
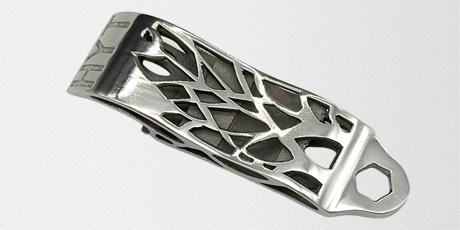
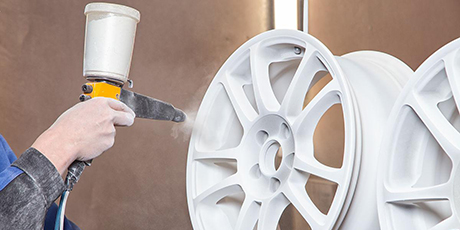
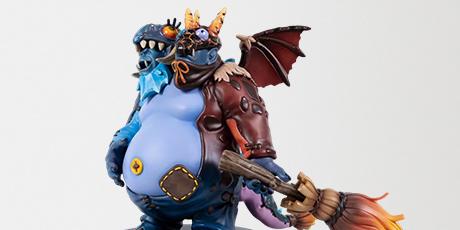
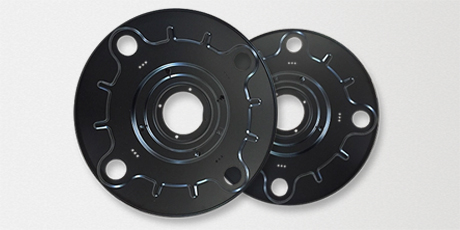
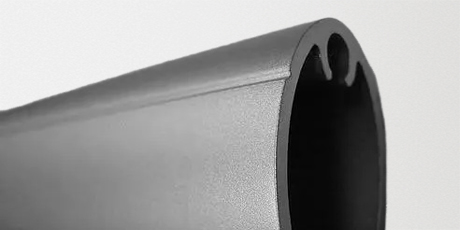
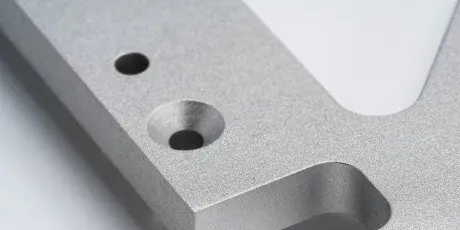
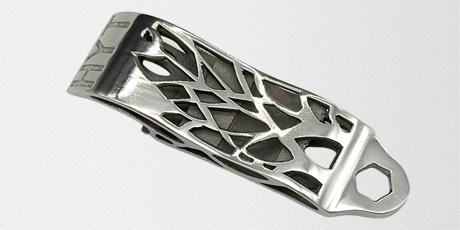
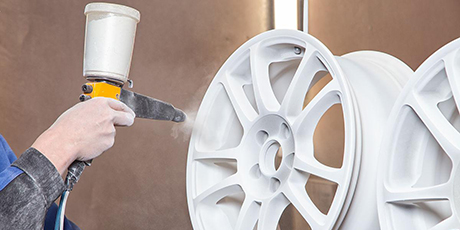
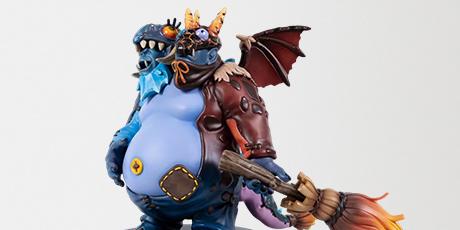
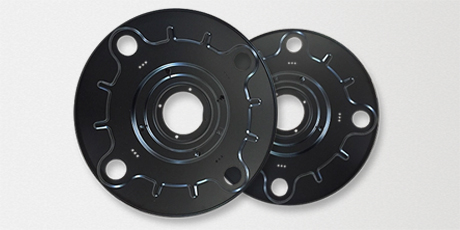
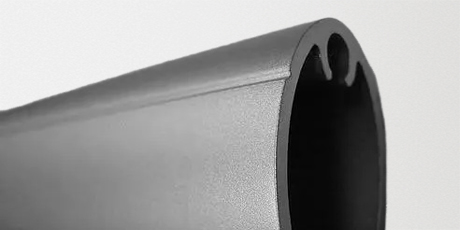
Parts Made by AutofabX
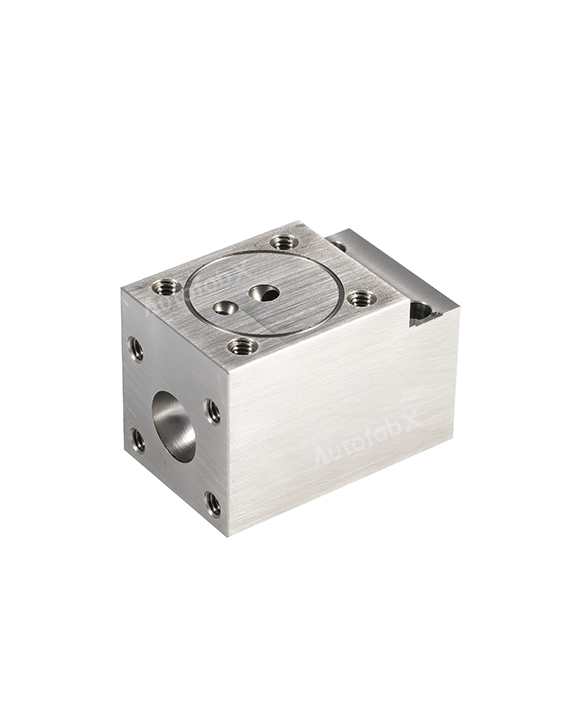
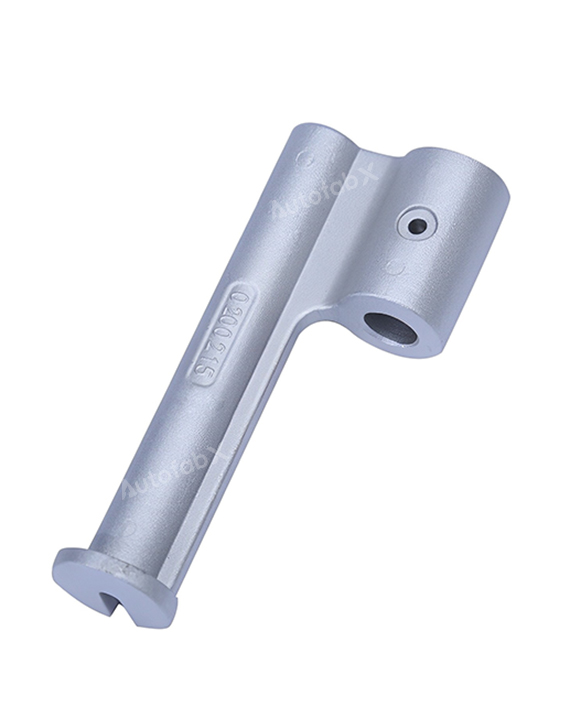