Custom Online Fused Deposition Modeling(FDM) Services
Material Variety, Precision and Quality, Cost-Effective, Expert Guidance
Start A New Quote
STEP | STP | IGS | DWG | DXF | PDF FilesFused Deposition Modeling(FDM) Materials
PC-FR(UL94-V0)
PC-FR(UL94-V0) could achieve V0 performance in the UL94 flame retardancy test and displays excellent toughness, strength and heat resistance. This filament opens new applications in the automotive, railway and aerospace industries.
Finishing:
Paint Glossy, Paint Matte, Silk Screen, Polishing
Overview
What is Fused Deposition Modeling (FDM)?
Fused Deposition Modeling (FDM) is an additive manufacturing process that uses a continuous filament of thermoplastic material, which is heated and extruded layer by layer to create a three-dimensional object. It is one of the most popular 3D printing technologies, known for its versatility and ease of use.
Why Choose AutofabX for FDM Services?
AutofabX provides high-quality FDM printing services with several advantages:
Material Variety: We offer a wide range of thermoplastics, including ABS, PLA, PETG, and advanced engineering plastics, to meet different application needs.
Precision and Quality: Our advanced FDM printers produce parts with excellent accuracy and consistent quality, suitable for both prototyping and functional end-use parts.
Cost-Effective: FDM is an economical choice for producing durable plastic parts, especially for prototyping and small-batch production.
Expert Guidance: Our team offers design optimization and material selection guidance to ensure the best results for FDM projects.
How Fused Deposition Modeling Works
Design: The process begins with a 3D CAD model, which is prepared in slicing software to create layer-by-layer instructions.
Heating and Extrusion: The thermoplastic filament is heated to a semi-liquid state and extruded through a nozzle.
Layer Deposition: The extruder moves along a defined path, depositing material layer by layer to build the part.
Cooling and Solidification: Each layer cools and solidifies before the next one is added, resulting in a fully formed part.
Main Equipment for FDM Printing and Popular Brands
Ultimaker S5: Known for its precision, reliability, and versatility, suitable for both prototyping and small production runs.
Stratasys F-Series: Offers high-quality prints and is widely used in industrial applications for functional prototyping and production.
MakerBot METHOD: Ideal for professional use, providing a balance of precision, material options, and ease of use.
Advantages and Limitations of FDM Printing
Advantages:
Material Variety: FDM can print with a wide range of thermoplastics, including high-performance materials.
Cost-Effective: FDM is one of the most affordable 3D printing technologies, ideal for prototyping and low-volume production.
Ease of Use: The process is simple and easy to use, making it accessible for both beginners and professionals.
Functional Parts: FDM produces durable parts that can be used for functional testing and end-use applications.
Limitations:
Surface Finish: FDM parts often have visible layer lines and may require post-processing to achieve a smooth finish.
Accuracy: The dimensional accuracy of FDM parts is lower compared to other 3D printing methods like SLA or SLS.
Anisotropy: FDM parts can be weaker along the Z-axis due to layer adhesion, which can impact mechanical properties.
Industry Applications and Case Studies for FDM Printing
Automotive Industry:
Application: Production of prototypes, jigs, and fixtures.
Case Study: An automotive manufacturer used FDM printing to create prototypes of interior components, allowing for rapid design iteration and cost savings.
Consumer Goods:
Application: Prototyping of consumer products and functional parts.
Case Study: A consumer electronics company used FDM to prototype enclosures for a new product, speeding up the development cycle.
Education:
Application: Teaching and learning tool for engineering and design students.
Case Study: A university utilized FDM printers in their engineering program to help students understand product design and prototyping.
Quality Control Standards and Inspection Methods for FDM Printing
Dimensional Inspection
Tools: Calipers and Coordinate Measuring Machines (CMM) are used to verify the dimensions of printed parts.
Surface Finish Inspection
Techniques: Visual inspection and surface roughness testers are used to ensure parts meet the required surface quality.
Mechanical Property Testing
Methods: Tensile and flexural tests are conducted to assess the strength and durability of printed parts.
FDM Printing Design Guidance Table
Design Aspect | Recommendation |
Minimum Wall Thickness | 1.2 mm |
Minimum Feature Size | 1.0 mm |
Overhangs | Use support for angles > 45° |
Tolerance | ±0.5 mm |
Layer Height | 100-300 microns |
FDM Printing Precision Table
Printing Process | Typical Tolerance |
FDM | ±0.5 mm |
Frequently Asked Questions (FAQs) about FDM Printing
What materials can be used in FDM printing?
FDM printing can use various thermoplastics, including PLA, ABS, PETG, TPU, and more advanced engineering plastics.
Is FDM printing suitable for functional parts?
Yes, FDM can produce functional parts, especially for applications requiring durability and impact resistance.
What industries benefit from FDM printing?
Industries such as automotive, consumer goods, and education benefit from the cost-effectiveness and versatility of FDM printing.
How accurate is FDM printing?
FDM printing can achieve tolerances of ±0.5 mm, which is sufficient for many prototyping and functional applications.
What post-processing is required for FDM-printed parts?
Post-processing may include sanding, painting, or vapor smoothing to improve surface finish and appearance.
Can FDM print with flexible materials?
Yes, FDM can print with flexible materials like TPU, which are useful for applications requiring elasticity.
How strong are FDM-printed parts?
The strength of FDM parts depends on the material used and the printing parameters, but they are generally suitable for functional prototypes and low-load applications.
Parts Made by AutofabX
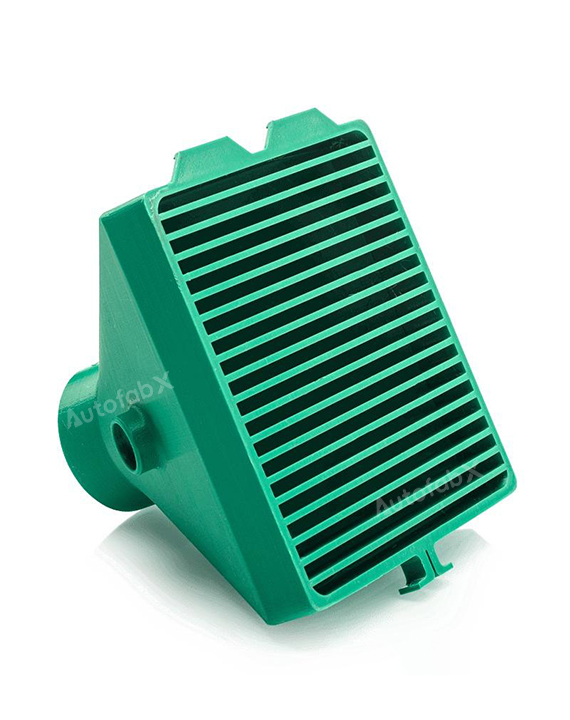
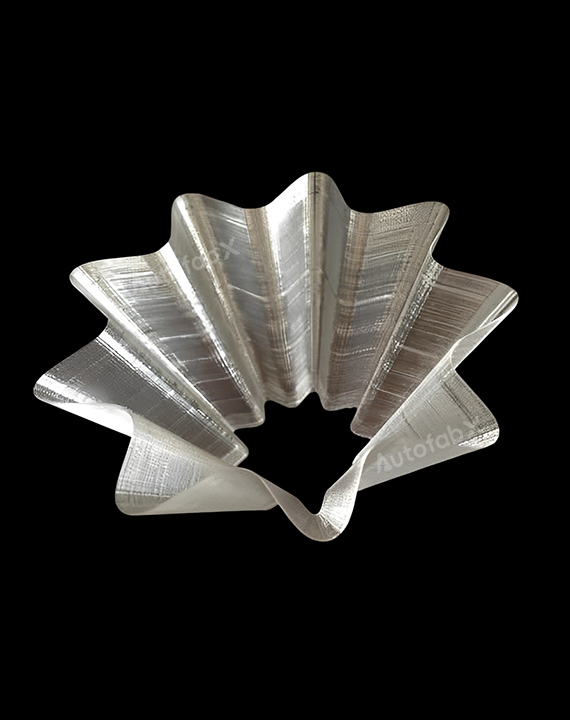
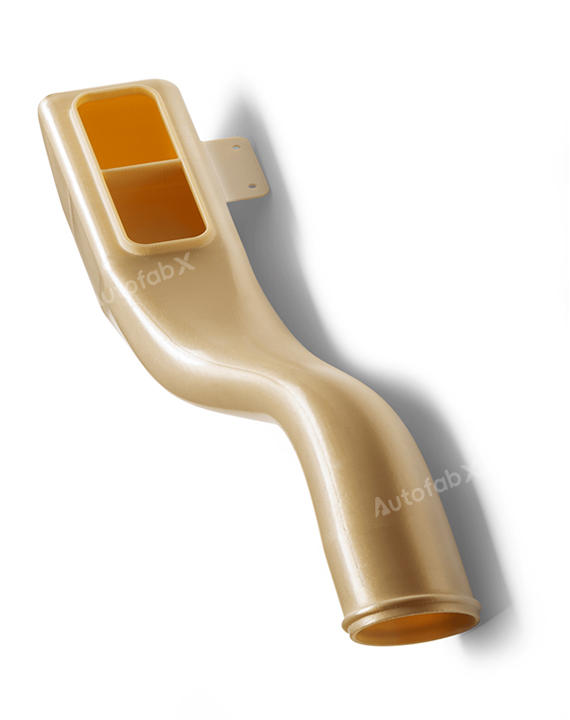
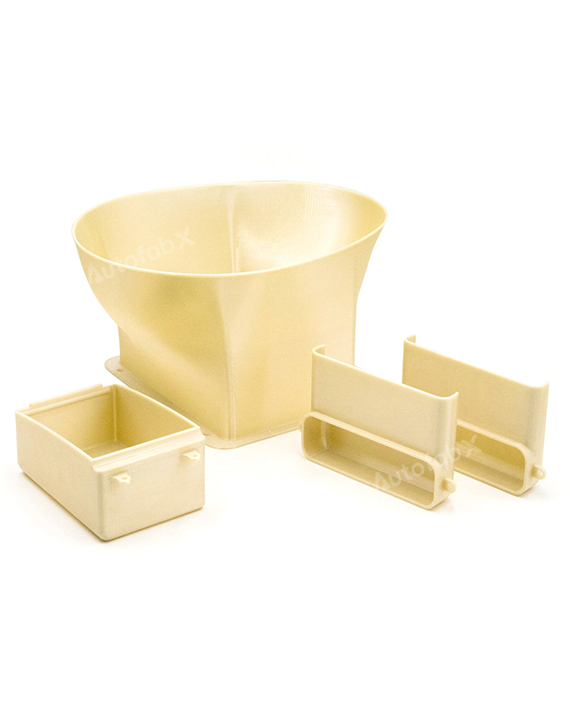
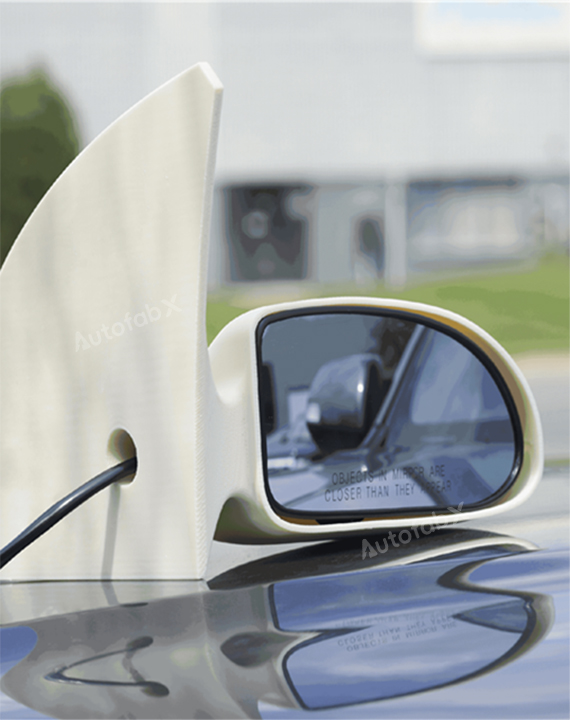
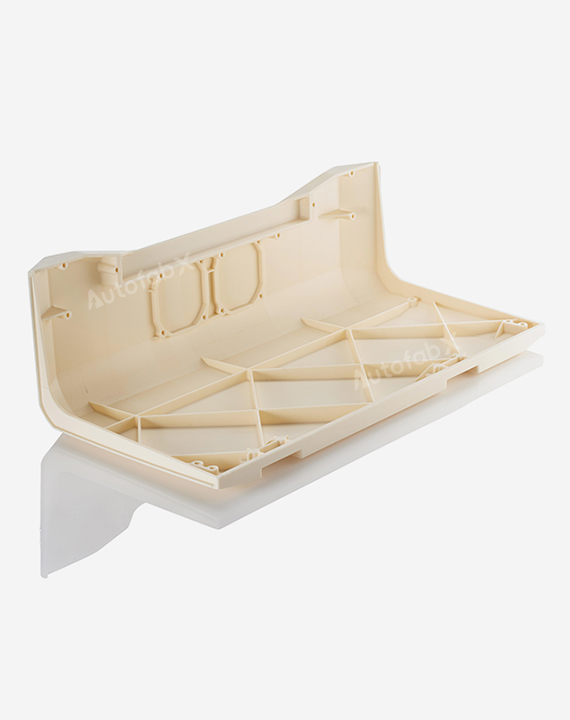
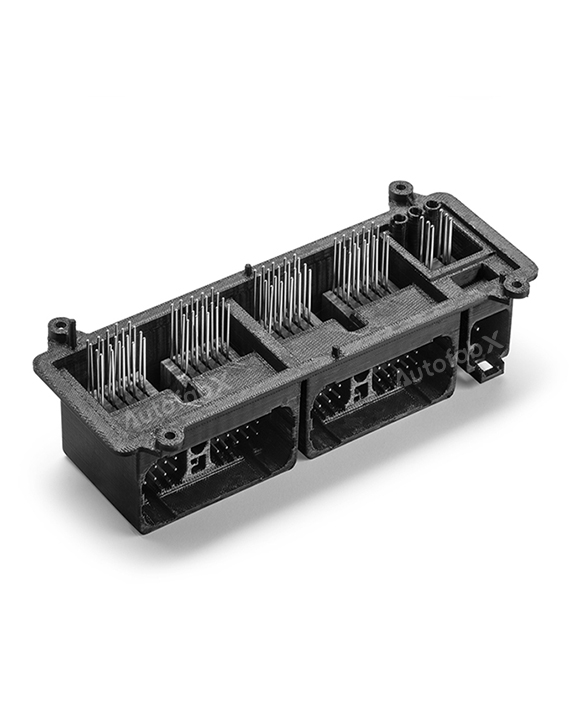
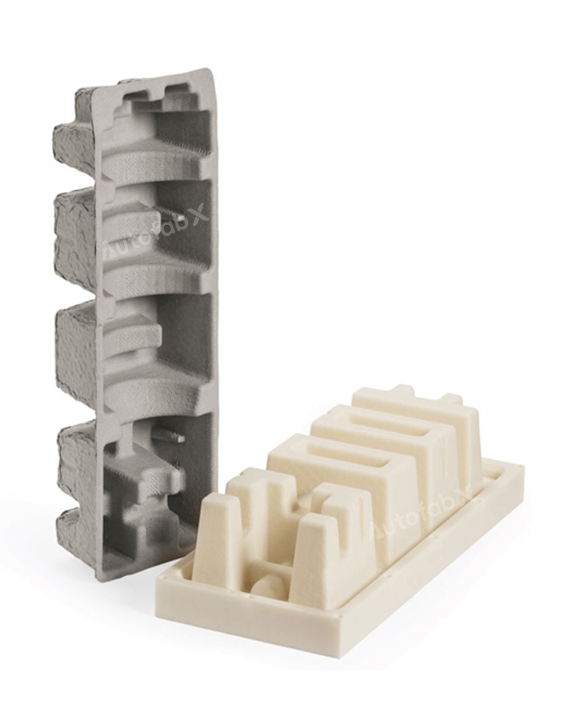
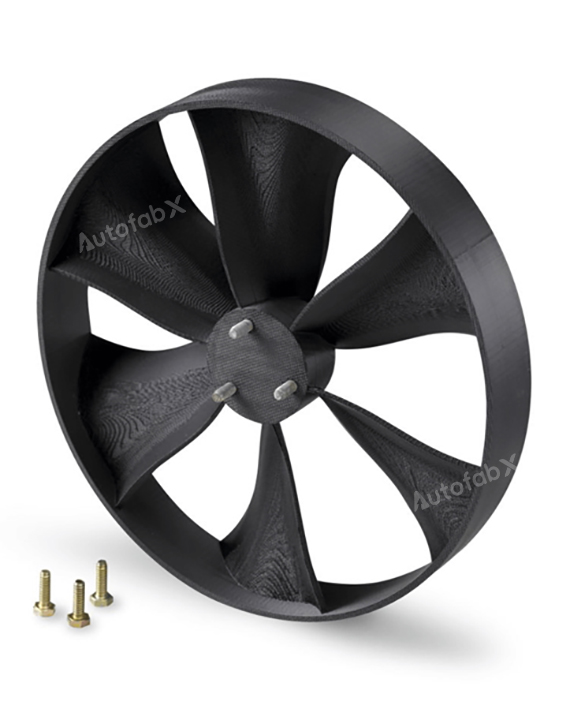
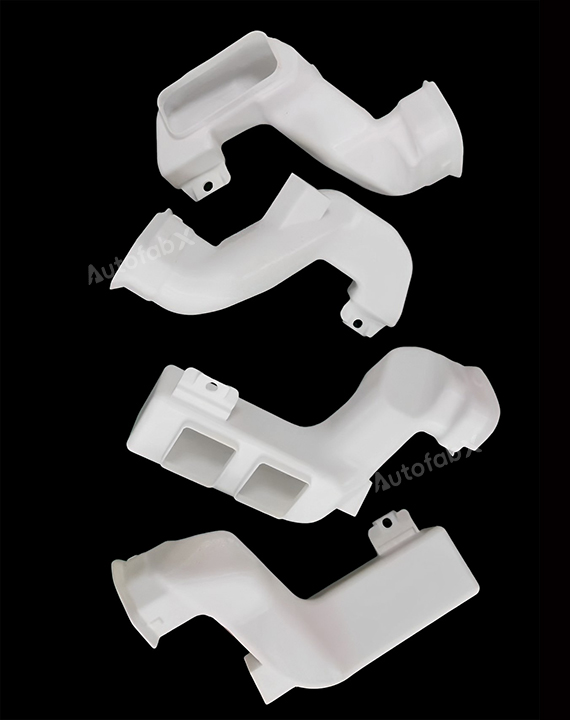
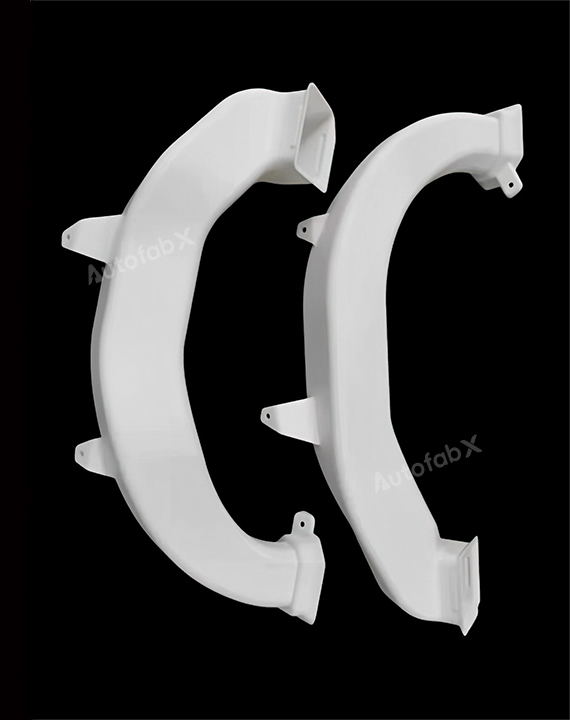
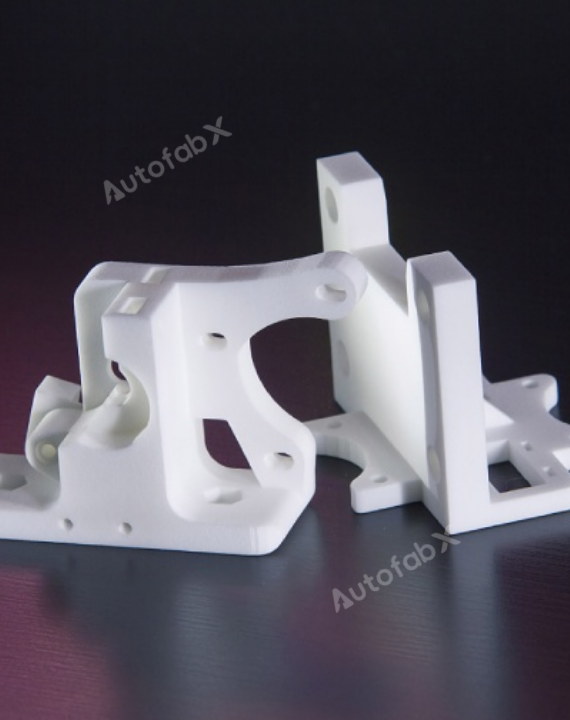
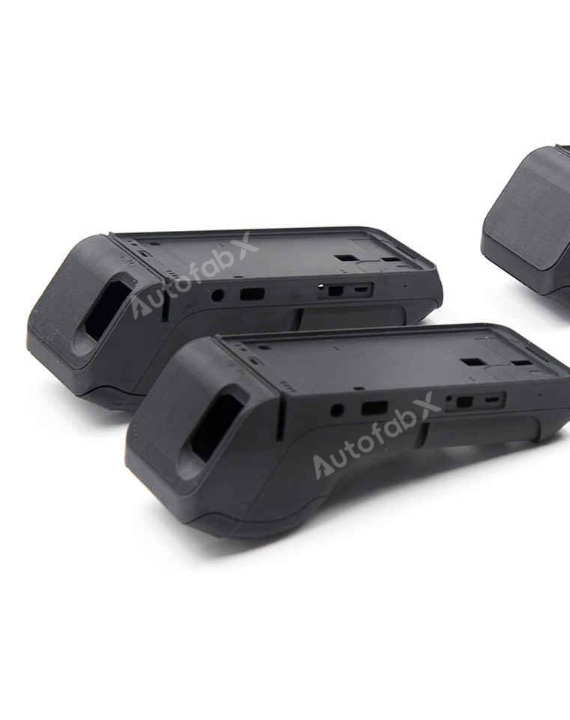
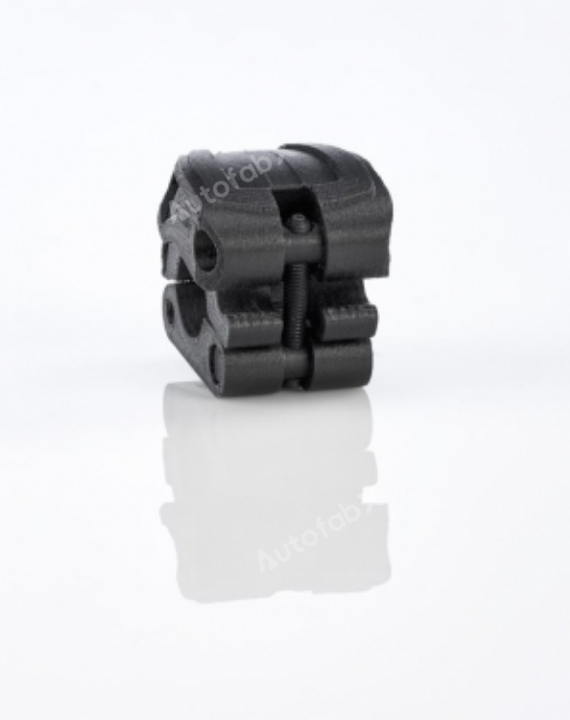
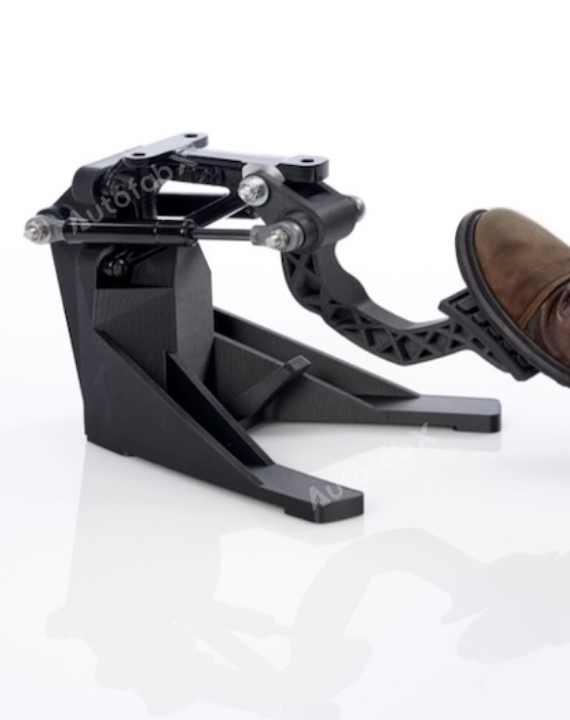
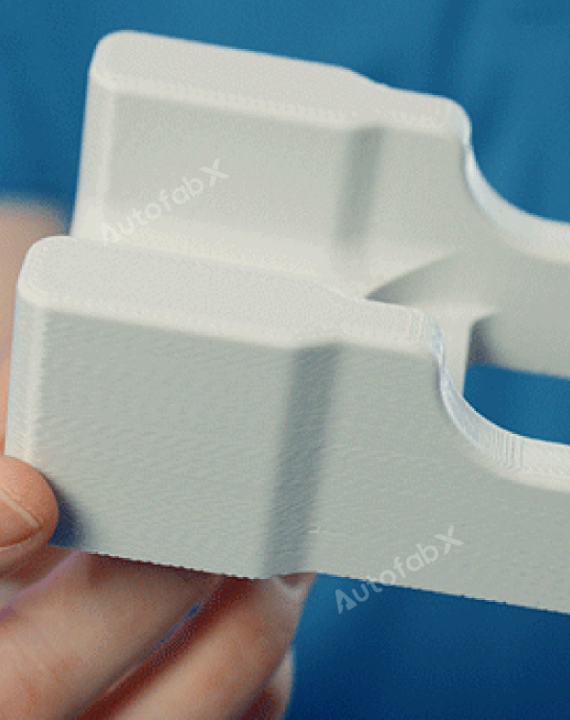