Custom Online CNC Milling Services
Get started with AutofabX's Instant CNC Milling Quotes. ISO 9001 and AS9100 certified quality at competitive prices.
Start A New Quote
STEP | STP | IGS | DWG | DXF | PDF FilesCNC Milling Materials
CNC Bronze Alloys
High Wear Resistance, Corrosion Resistance, Excellent Machinability
Finishing:
Passivating, Powder Coating, Electropolishing, Zinc Plating, Silver Plating, Gold Plating, Electroless Nickel Plating, Bead Blasting, Tempering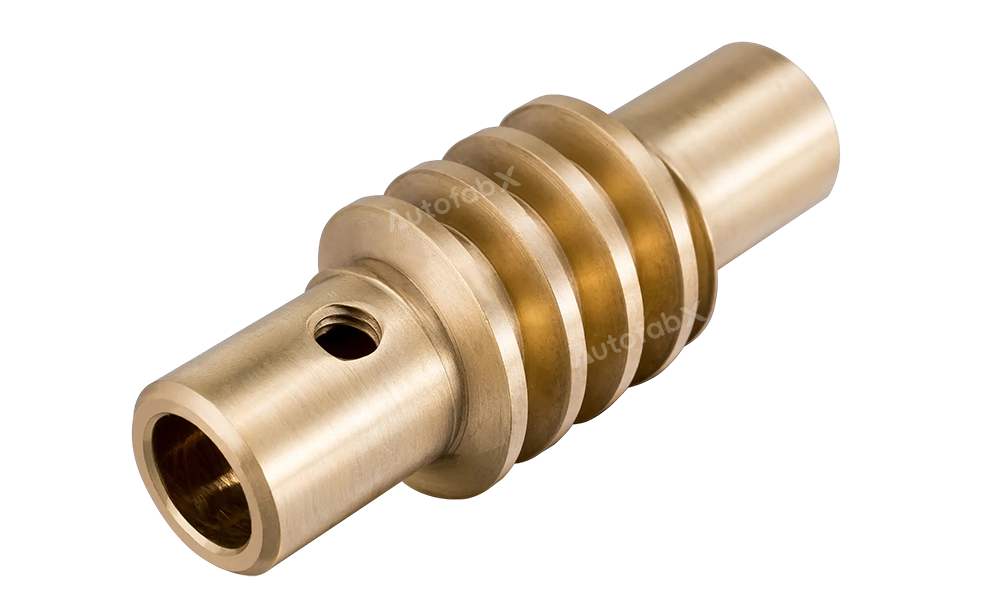
Overview
What is CNC Milling?
CNC (Computer Numerical Control) milling is a manufacturing process that uses rotary cutters to remove material from a workpiece, creating parts with complex shapes and features. CNC milling is one of the most widely used machining processes due to its versatility and precision, capable of producing components from a wide variety of materials, including metals, plastics, and composites.
Why Choose AutofabX for CNC Milling Services?
AutofabX offers high-quality CNC milling services with advanced capabilities to meet the needs of various industries. Reasons to choose AutofabX include:
State-of-the-Art Machinery: We use the latest CNC milling machines to ensure high precision and consistency.
Expert Engineering Team: Our experienced engineers provide design support, optimizing parts for manufacturability and quality.
Custom Solutions: Whether for prototyping or mass production, we provide flexible solutions tailored to your needs.
Stringent Quality Control: We implement strict quality assurance procedures to ensure each part meets industry standards.
How CNC Milling Works and the Process Steps
CNC milling works by using programmed instructions to control the movement of cutting tools and the workpiece. The basic steps involved in the CNC milling process are:
CAD Design: The part is designed using CAD software, generating a detailed 3D model.
CAM Programming: The CAD model is translated into CAM (Computer-Aided Manufacturing) software, which generates the toolpaths and instructions for milling.
Machine Setup: The material is secured in the machine, and the appropriate cutting tools are selected and installed.
Milling: The CNC milling machine follows the programmed toolpaths to remove material and create the part.
Finishing: Secondary processes, such as deburring or polishing, may be applied to achieve the desired surface quality.
Main Equipment for CNC Milling and Popular Brands
Vertical CNC Milling Machines
Leading Brands: Haas, DMG Mori, Mazak, FANUC
Horizontal CNC Milling Machines
Leading Brands: Okuma, Makino, Doosan
Multi-Axis CNC Milling Machines
Leading Brands: Hermle, CNC Masters, Hurco
CNC Tooling and Fixtures
Leading Brands: Kennametal, Sandvik Coromant, Iscar
Advantages and Limitations of CNC Milling
Advantages:
High Precision and Accuracy: CNC milling allows for extremely tight tolerances, making it suitable for high-precision parts.
Complex Geometry Capability: CNC milling can produce intricate designs and features that are difficult to achieve with other methods.
Material Versatility: CNC milling can work with a wide range of materials, including metals, plastics, and composites.
Scalability: Suitable for both small-batch prototypes and large-volume production runs.
Repeatability: CNC milling offers consistent and repeatable results, ensuring high-quality parts.
Limitations:
Cost: CNC milling can be costly, especially for custom or low-volume parts, due to setup and tooling costs.
Material Waste: As a subtractive process, CNC milling generates material waste, which may increase production costs.
Complex Internal Features: Some internal features and geometries may not be achievable with CNC milling alone.
Industry Applications and Case Studies for CNC Milling
Aerospace Industry:
Application: Production of turbine blades, brackets, and structural components.
Case Study: An aerospace company used CNC milling to manufacture precision-engineered turbine blades, ensuring high performance and safety.
Automotive Industry:
Application: Manufacturing of engine components, transmission parts, and brackets.
Case Study: An automotive manufacturer utilized CNC milling to produce lightweight yet durable engine components, improving fuel efficiency.
Medical Industry:
Application: Production of surgical instruments, prosthetics, and implants.
Case Study: A medical device company used CNC milling to create biocompatible stainless steel implants, ensuring patient safety and precision fit.
Quality Control Standards and Inspection Methods for CNC Milling
Dimensional Inspection
Tools: Coordinate Measuring Machines (CMM), calipers, and micrometers are used to verify the dimensions of the machined parts.
Surface Finish Inspection
Techniques: Visual inspection and surface roughness testers ensure that the surface finish meets the specified requirements.
Material Property Testing
Methods: Hardness testing, tensile testing, and material composition analysis are conducted to verify material properties.
Non-Destructive Testing (NDT)
Methods: Ultrasonic testing and dye penetrant inspection are used to detect internal defects or surface cracks.
CNC Milling Design Guidance Table
Design Aspect | Recommendation |
Minimum Wall Thickness | 1.0 mm |
Minimum Drill Hole Size | 0.8 mm |
Maximum Part Size | 1000 mm x 500 mm x 500 mm |
Tolerances | ±0.05 mm |
Corner Radii | Minimum 0.5 mm radius |
Thread Depth | Max depth of 3x the diameter |
Surface Finish | Specify requirements based on application |
CNC Milling Precision Table
Machining Operation | Typical Tolerance |
Milling | ±0.05 mm |
Drilling | ±0.08 mm |
Finishing | ±0.02 mm |
Frequently Asked Questions (FAQs) about CNC Milling
What materials can be used in CNC milling?
CNC milling can machine a variety of materials, including metals (aluminum, steel, titanium), plastics (ABS, polycarbonate), and composites.
How does CNC milling differ from CNC turning?
CNC milling uses rotary cutters to remove material, while CNC turning rotates the workpiece against a stationary cutting tool, making it ideal for cylindrical parts.
What is the typical lead time for CNC milling?
Lead times vary depending on part complexity and volume but typically range from 3 to 10 business days.
How precise is CNC milling?
CNC milling can achieve tolerances as tight as ±0.01 mm, depending on the specific requirements of the part.
Can CNC milling be used for prototyping?
Yes, CNC milling is commonly used for prototyping, especially when high precision and material versatility are needed.
What industries use CNC milling?
CNC milling is used in industries such as aerospace, automotive, medical, electronics, and consumer products.
How can I ensure my part is suitable for CNC milling?
Ensure your design follows guidelines such as maintaining uniform wall thickness, including corner radii to reduce stress concentrations, and specifying realistic tolerances.
Parts Made by AutofabX
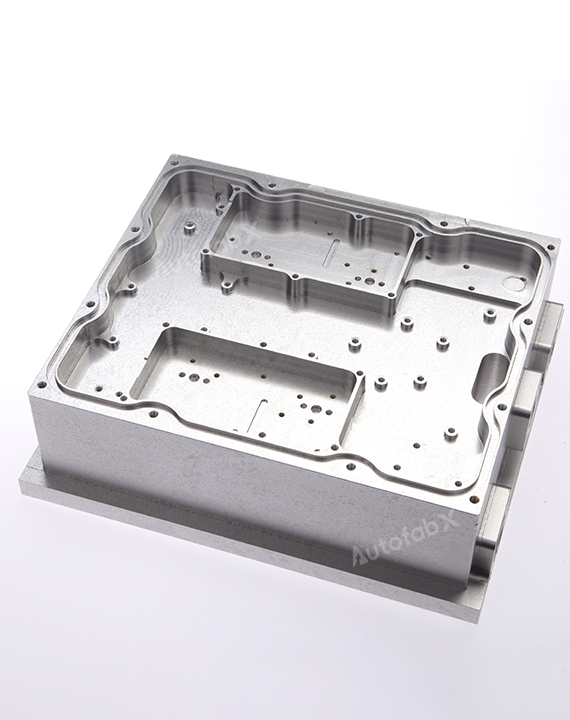
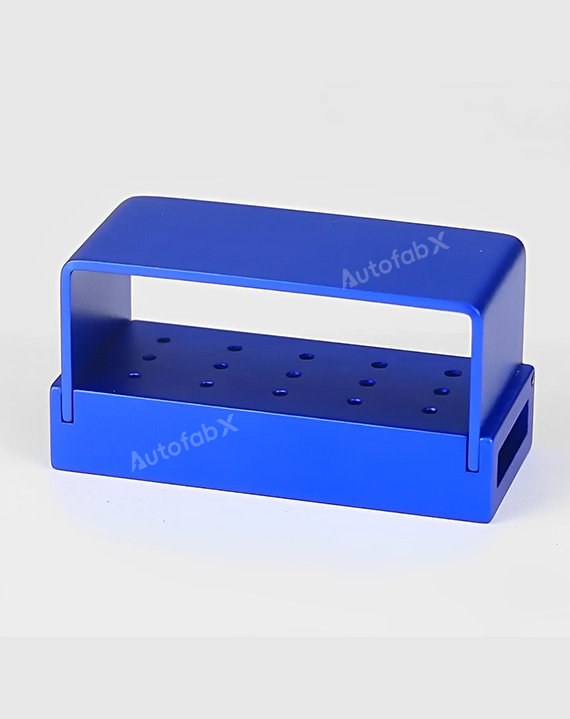


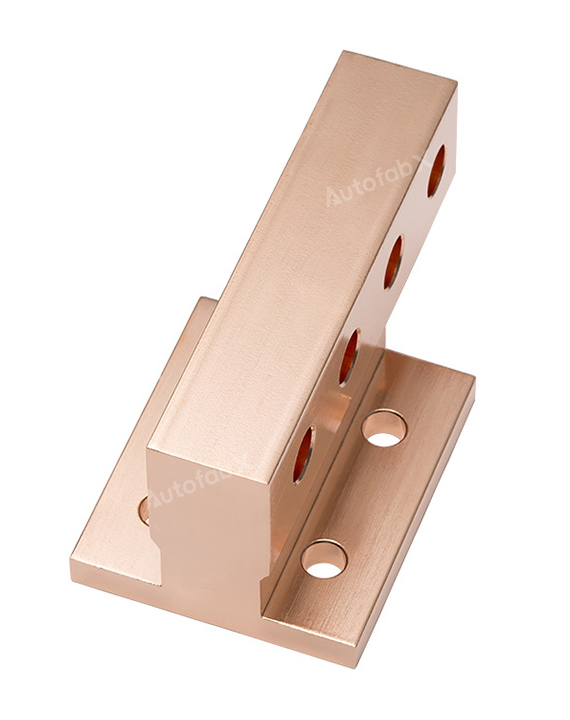
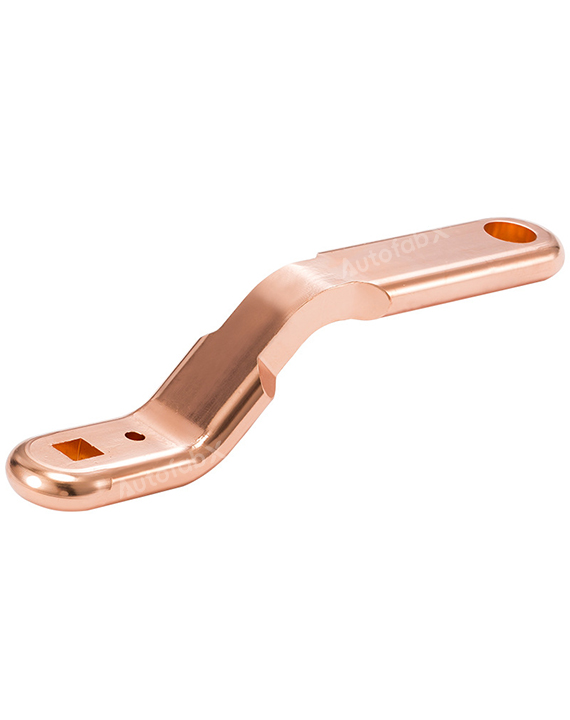
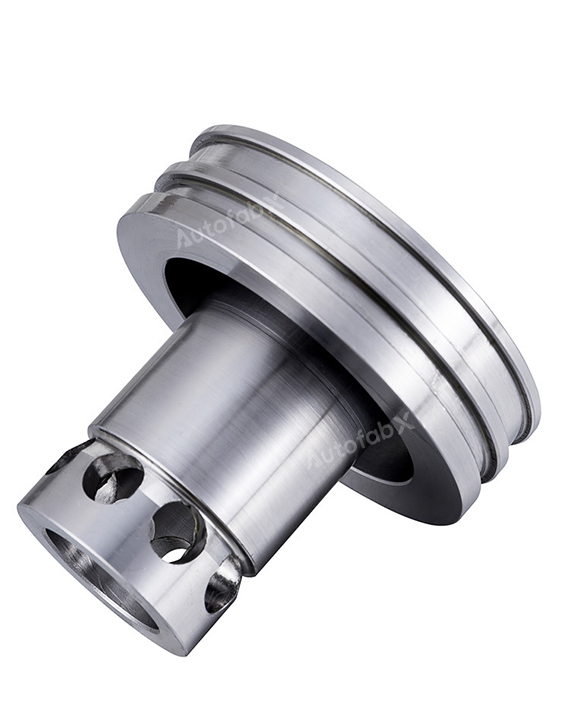
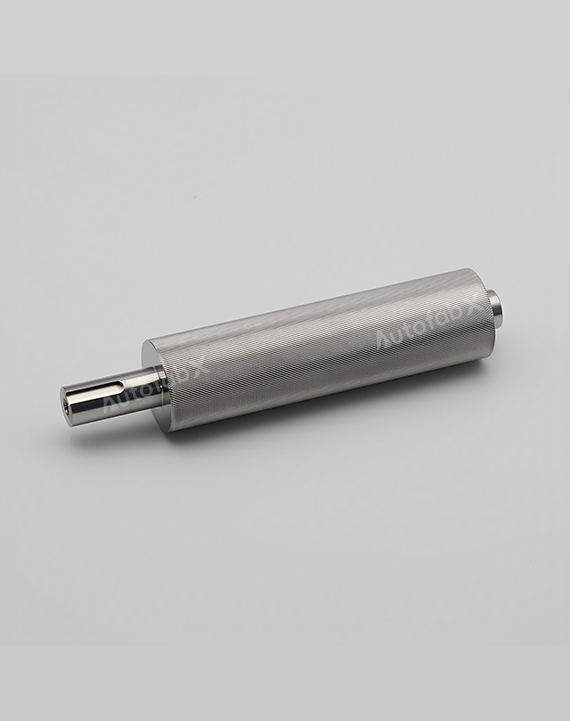
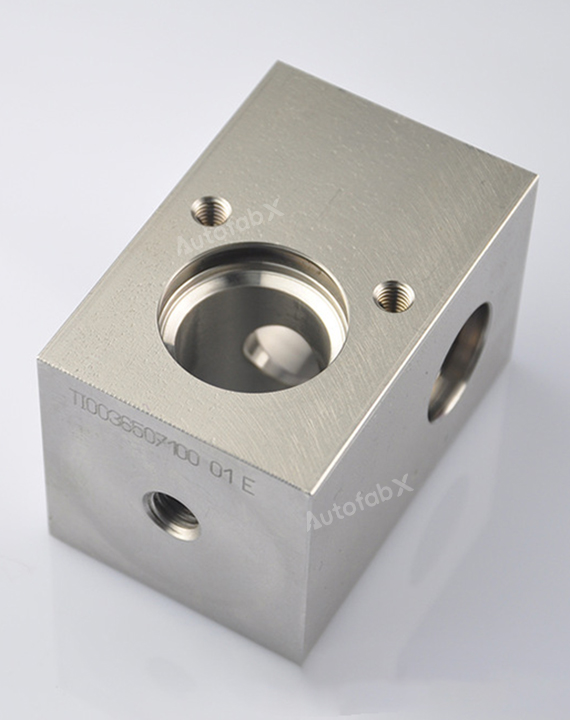
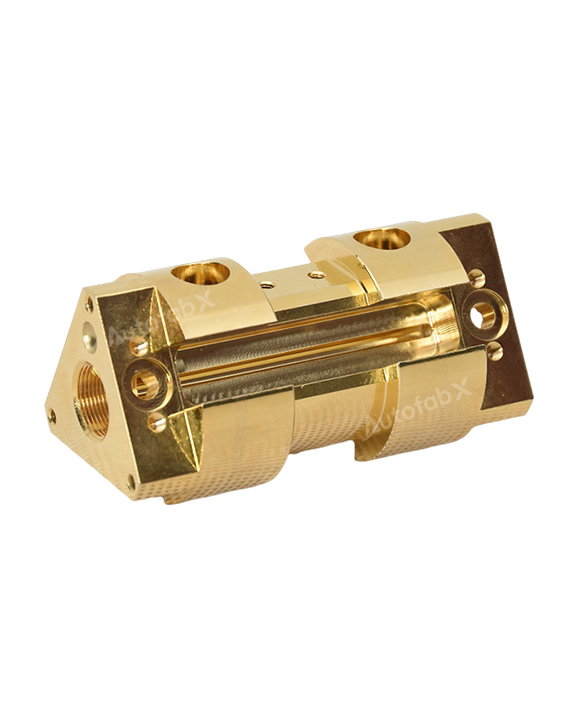
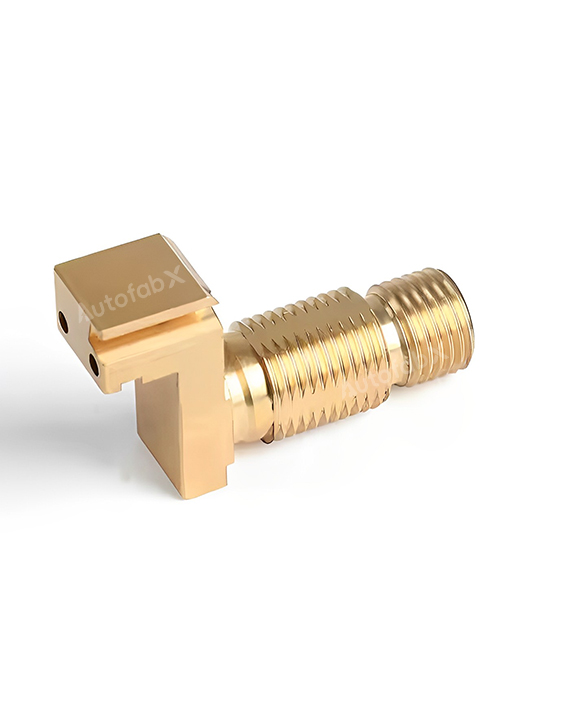
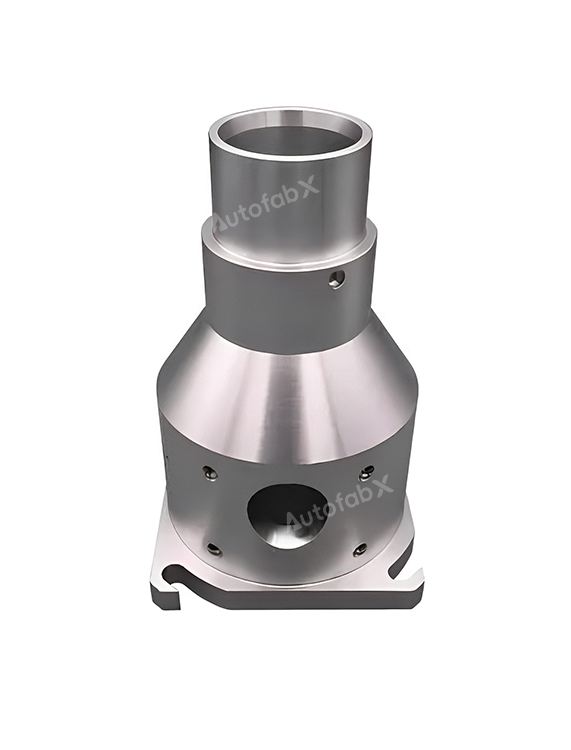
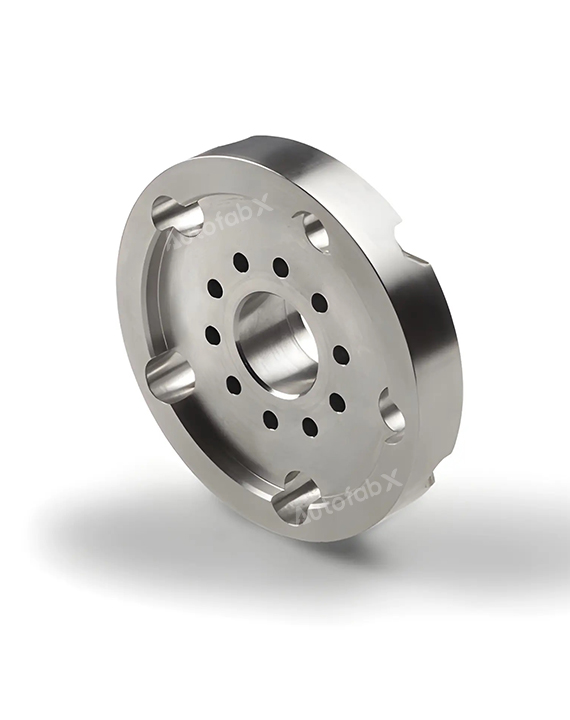
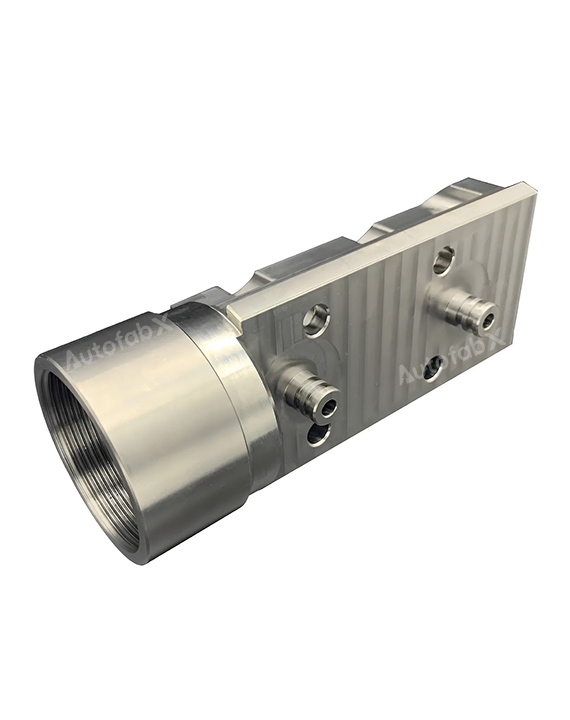
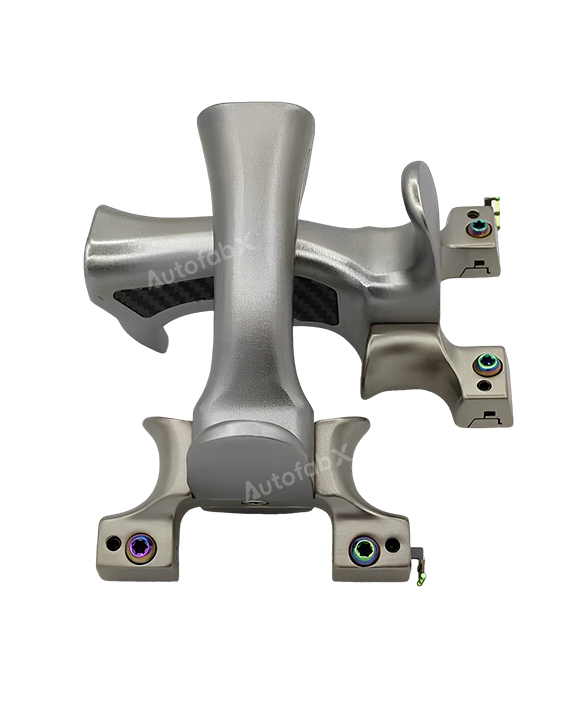

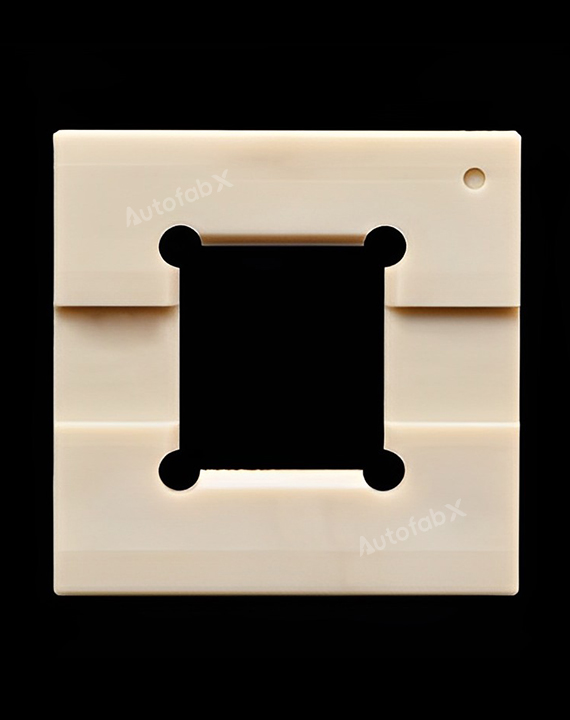
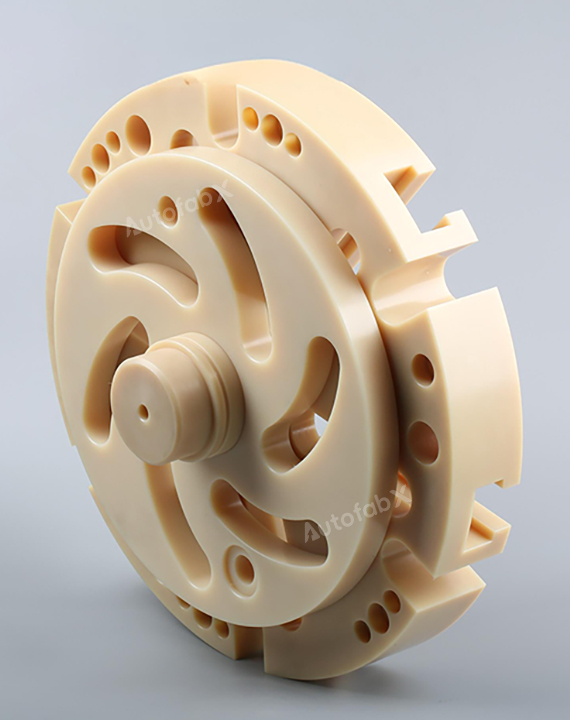
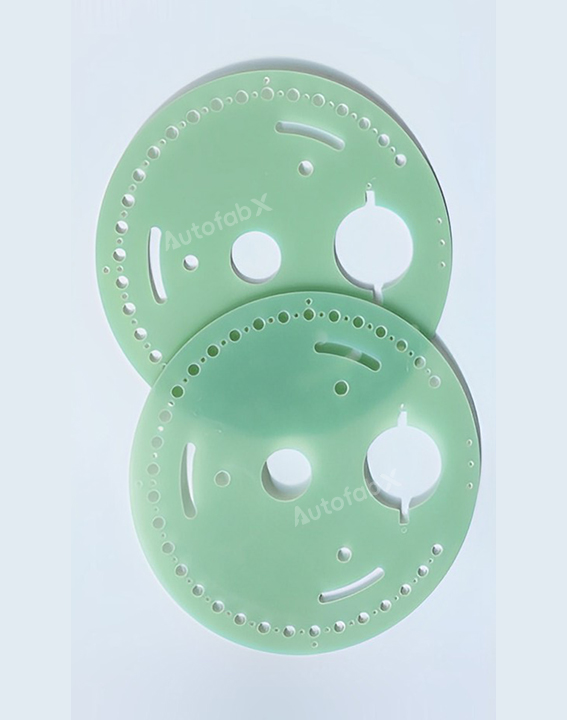
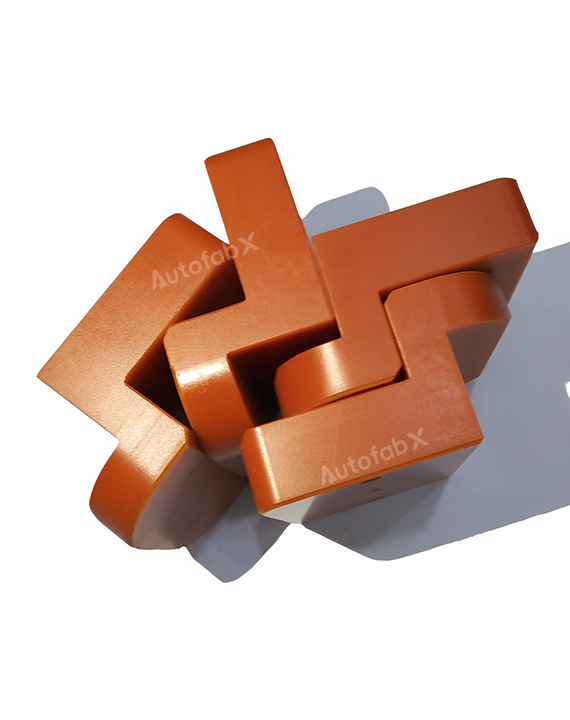
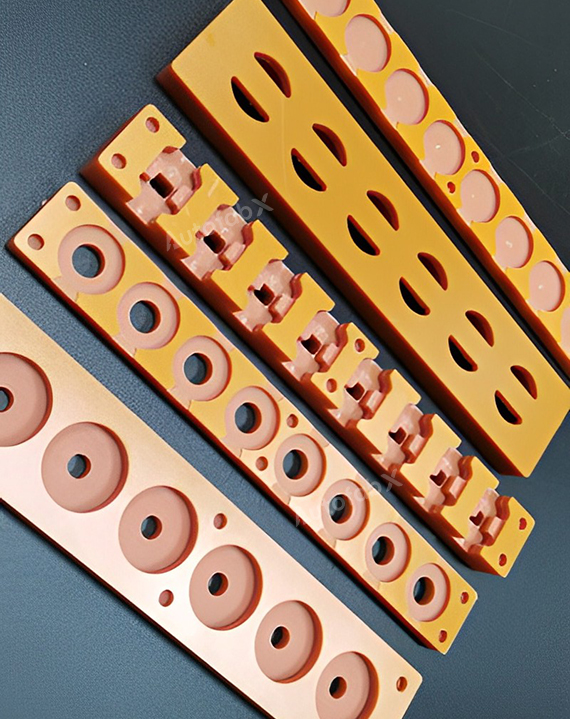
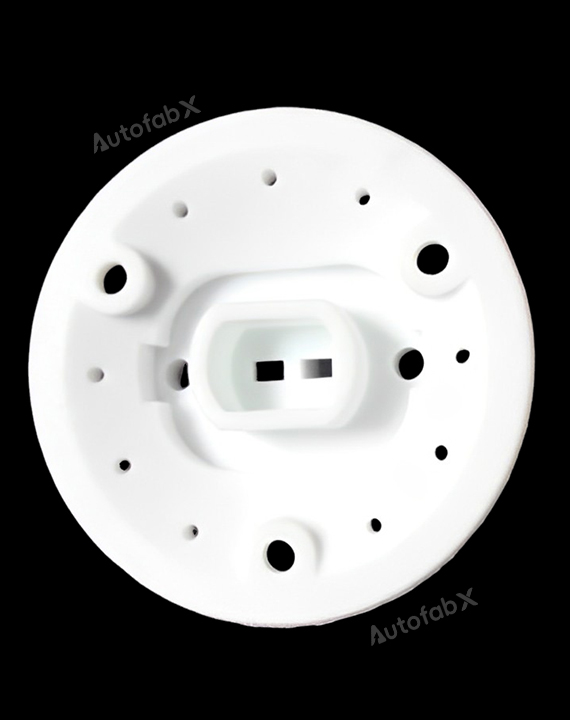
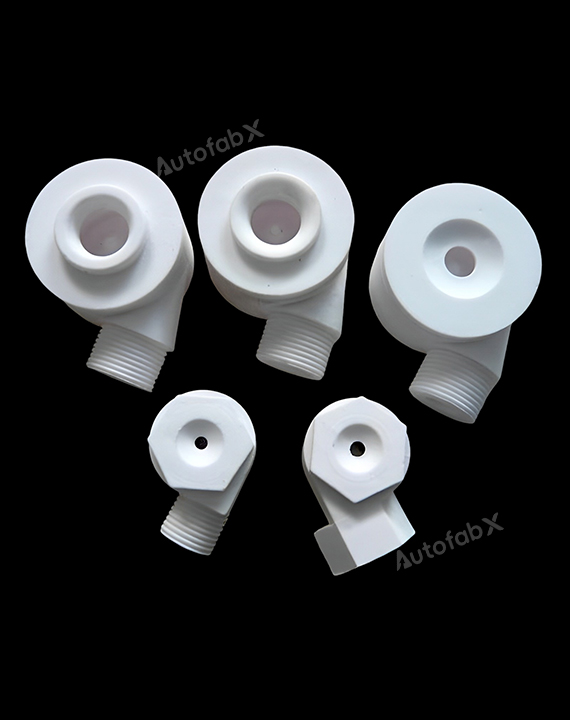
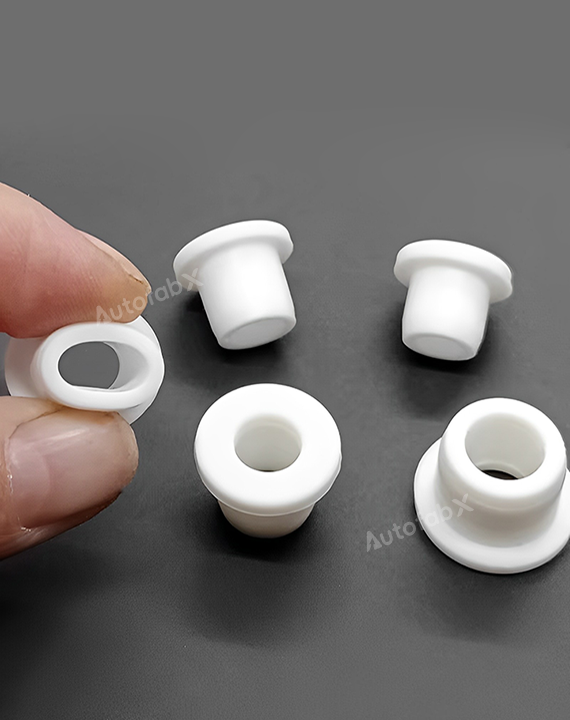
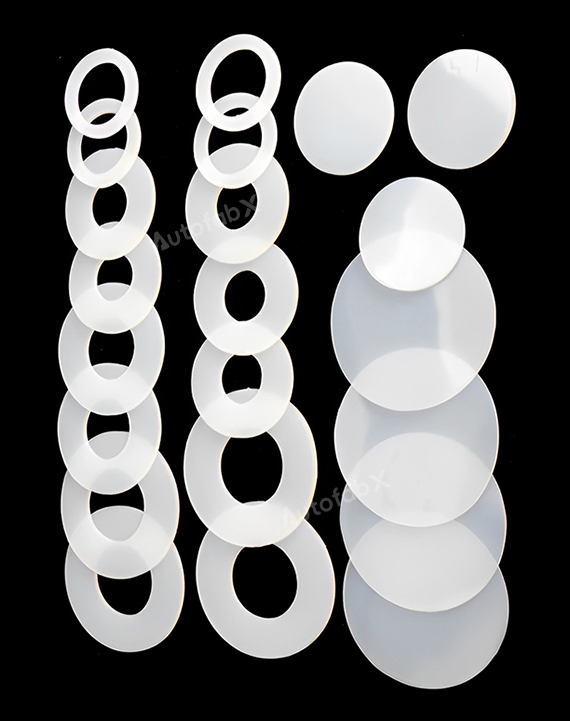