Custom Online CNC Turning Services
Precise CNC turning from AutofabX with ISO certified quality. Get your instant quote today!
Start A New Quote
STEP | STP | IGS | DWG | DXF | PDF FilesCNC Turning Materials
CNC Bronze Alloys
High Wear Resistance, Corrosion Resistance, Excellent Machinability
Finishing:
Passivating, Powder Coating, Electropolishing, Zinc Plating, Silver Plating, Gold Plating, Electroless Nickel Plating, Bead Blasting, Tempering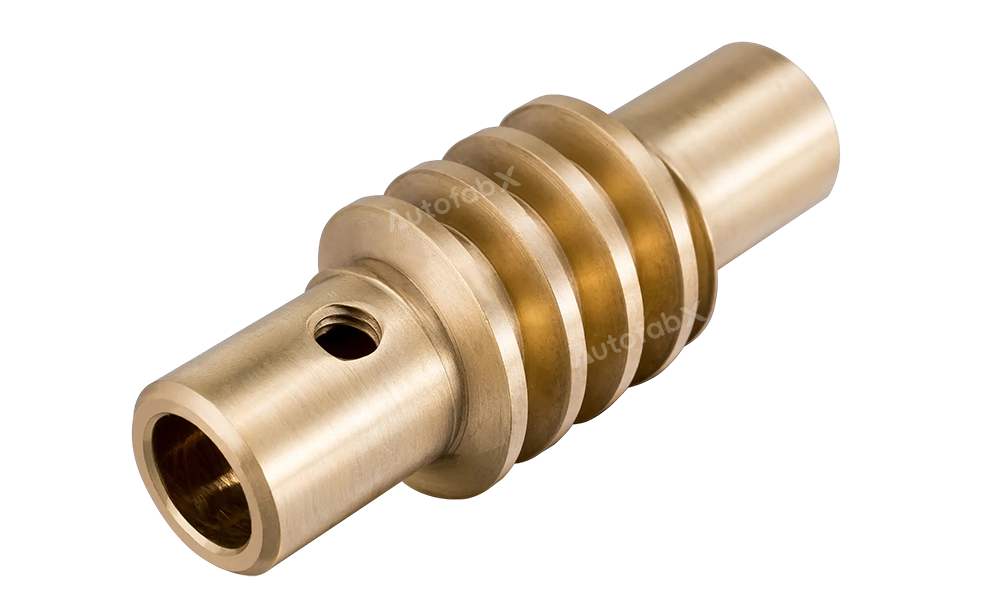
Overview
What is CNC Turning?
CNC (Computer Numerical Control) turning is a machining process in which a cutting tool moves along the surface of a rotating workpiece to remove material and shape it. It is typically used to produce cylindrical parts such as shafts, bolts, and rings. CNC turning offers high precision and repeatability, making it a preferred method for creating consistent components.
Why Choose AutofabX for CNC Turning Services?
AutofabX provides high-quality CNC turning services with a focus on precision, efficiency, and customization. Reasons to choose AutofabX include:
Modern Equipment: We use the latest CNC lathes to ensure precision and speed.
Experienced Engineers: Our team of experts works with clients to optimize part design for manufacturability.
Flexible Production: From prototypes to full-scale production, we can handle orders of any size.
Quality Assurance: Stringent quality checks are performed to ensure every part meets specifications.
How CNC Turning Works and the Process Steps
CNC turning works by rotating the workpiece while a stationary cutting tool removes material to create the desired shape. The main steps in the CNC turning process are:
CAD Design: The part is designed using CAD software to create a precise model.
CAM Programming: The CAD model is converted into CAM software, which generates toolpaths and cutting instructions.
Machine Setup: The workpiece is mounted on the CNC lathe, and the appropriate tooling is selected.
Turning: The CNC machine rotates the workpiece while the cutting tool removes material, shaping the part.
Finishing: Secondary operations such as polishing or threading may be performed to achieve the desired finish.
Main Equipment for CNC Turning and Popular Brands
CNC Lathes
Leading Brands: Haas, Okuma, Mazak, DMG Mori
Multi-Axis CNC Lathes
Leading Brands: Doosan, Hurco, Nakamura-Tome
Tooling and Accessories
Leading Brands: Sandvik Coromant, Kennametal, Iscar
Advantages and Limitations of CNC Turning
Advantages:
High Precision: CNC turning offers tight tolerances, making it ideal for precision components.
Fast Production: CNC lathes can quickly produce parts, especially in high-volume runs.
Versatility: Capable of handling a wide range of materials, from metals to plastics.
Consistent Quality: Automated control ensures repeatability and consistent part quality.
Limitations:
Limited Geometries: CNC turning is best suited for cylindrical or symmetrical parts; complex non-cylindrical shapes may require additional processes.
Material Waste: As a subtractive process, CNC turning generates material waste, which can be costly for expensive materials.
Setup Costs: Initial setup and programming can be time-consuming, particularly for small production runs.
Industry Applications and Case Studies for CNC Turning
Automotive Industry:
Application: Production of drive shafts, gears, and fasteners.
Case Study: An automotive manufacturer used CNC turning to produce precision gears, ensuring durability and smooth performance.
Aerospace Industry:
Application: Manufacturing of turbine components, bushings, and fittings.
Case Study: CNC turning was used to create high-precision bushings for aerospace applications, meeting strict safety and performance standards.
Medical Industry:
Application: Production of bone screws, surgical tools, and implants.
Case Study: A medical device company utilized CNC turning to manufacture titanium bone screws, ensuring biocompatibility and accuracy.
Quality Control Standards and Inspection Methods for CNC Turning
Dimensional Inspection
Tools: Coordinate Measuring Machines (CMM), calipers, and micrometers are used to verify the accuracy of the turned parts.
Surface Finish Inspection
Techniques: Visual inspection and surface roughness testers ensure that the surface finish meets the specified requirements.
Material Property Testing
Methods: Hardness testing and tensile testing are conducted to ensure material properties meet specifications.
Non-Destructive Testing (NDT)
Methods: Ultrasonic testing and dye penetrant inspection are used to detect internal defects or surface cracks.
CNC Turning Design Guidance Table
Design Aspect | Recommendation |
Minimum Wall Thickness | 1.5 mm |
Minimum Drill Hole Size | 1.0 mm |
Maximum Part Length | 1000 mm |
Tolerances | ±0.02 mm |
Thread Depth | Max depth of 2x the diameter |
Surface Finish | Specify requirements based on application |
CNC Turning Precision Table
Machining Operation | Typical Tolerance |
Turning | ±0.02 mm |
Drilling | ±0.05 mm |
Threading | ±0.03 mm |
Frequently Asked Questions (FAQs) about CNC Turning
What materials can be used in CNC turning?
CNC turning can work with metals (aluminum, steel, brass), plastics (nylon, PTFE), and composites.
What is the difference between CNC turning and CNC milling?
CNC turning rotates the workpiece against a cutting tool, ideal for cylindrical parts, whereas CNC milling involves moving the cutting tool to remove material from a stationary workpiece.
How precise is CNC turning?
CNC turning can achieve tolerances as tight as ±0.01 mm, depending on the part requirements.
Is CNC turning suitable for prototyping?
Yes, CNC turning is suitable for prototyping, especially for cylindrical components that require high precision.
What industries use CNC turning?
CNC turning is used in industries such as automotive, aerospace, medical, and consumer products.
How can I ensure my design is suitable for CNC turning?
Ensure your design follows best practices such as maintaining uniform wall thickness, specifying appropriate tolerances, and designing with cylindrical features in mind.
What is the typical lead time for CNC turning?
Lead times vary based on part complexity and volume but generally range from 3 to 7 business days.
Parts Made by AutofabX
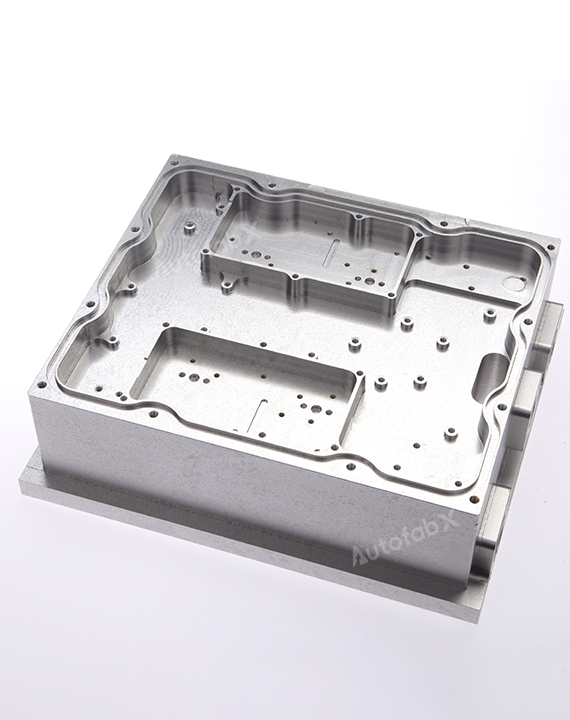
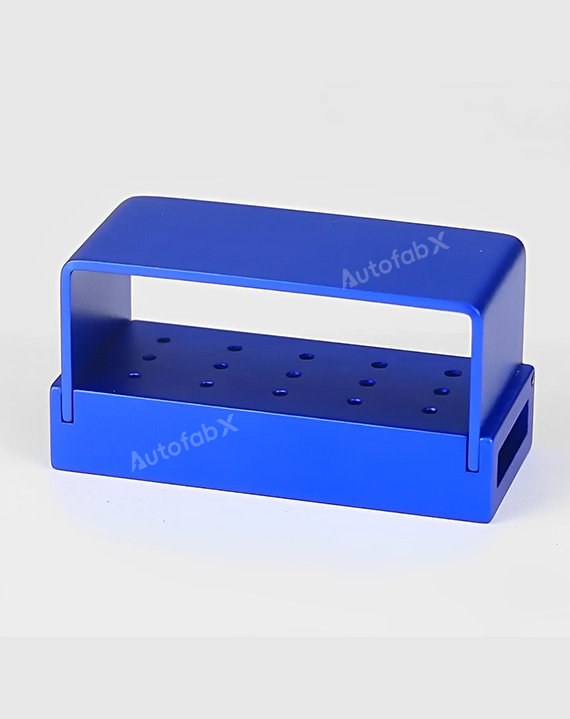


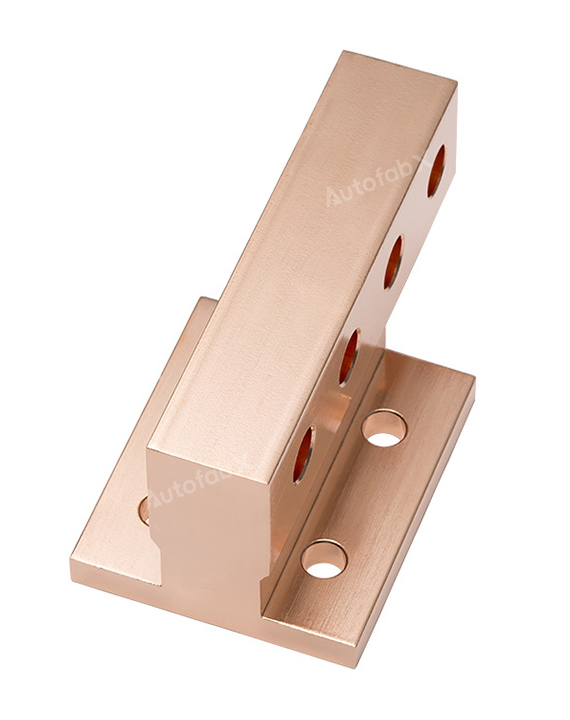
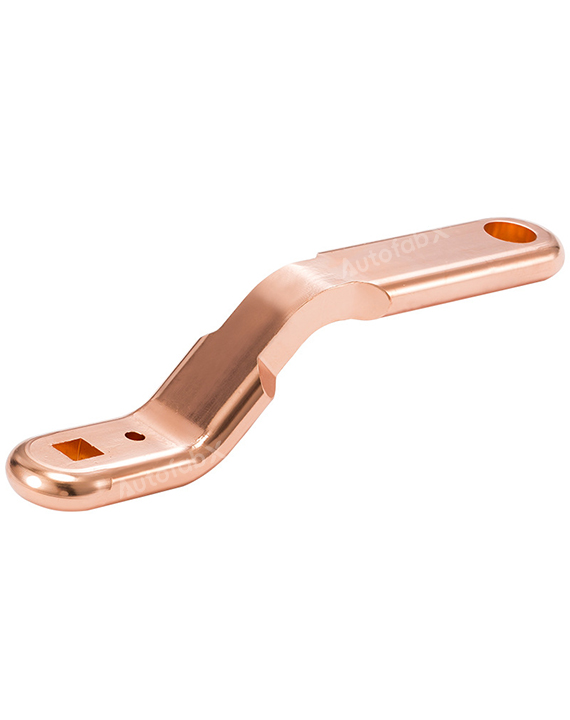
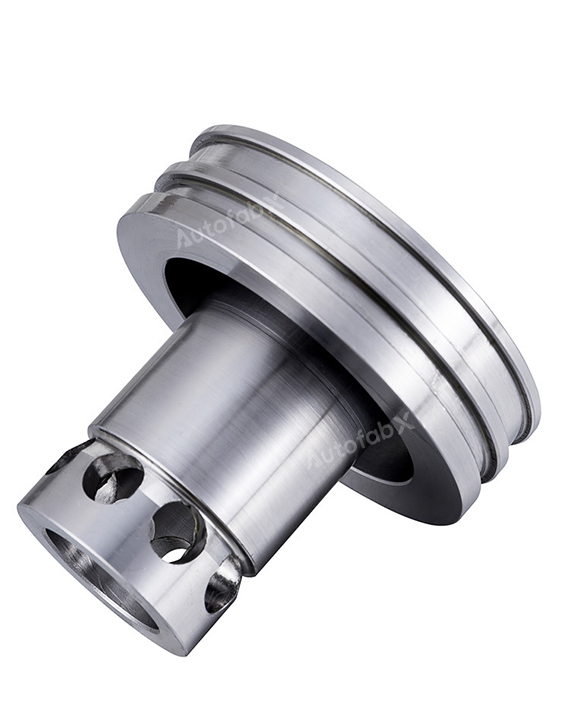
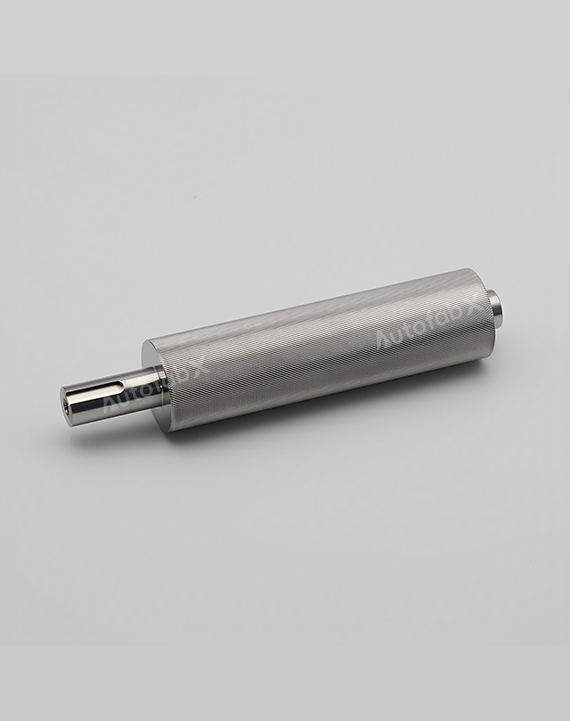
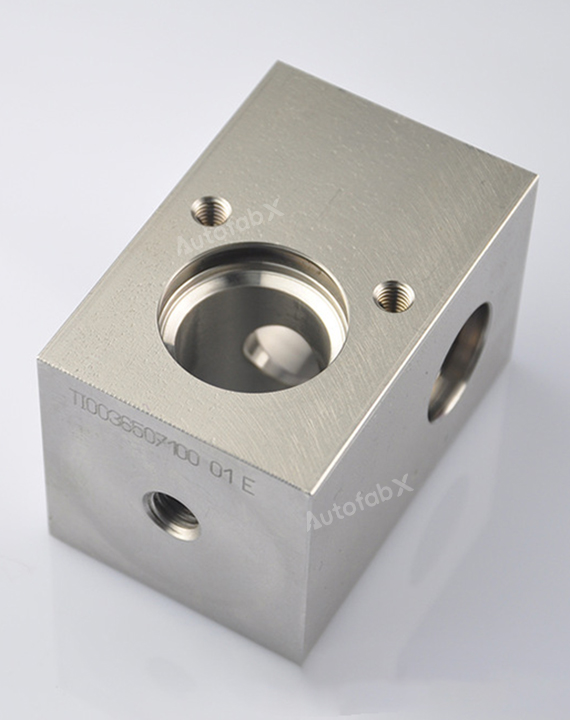
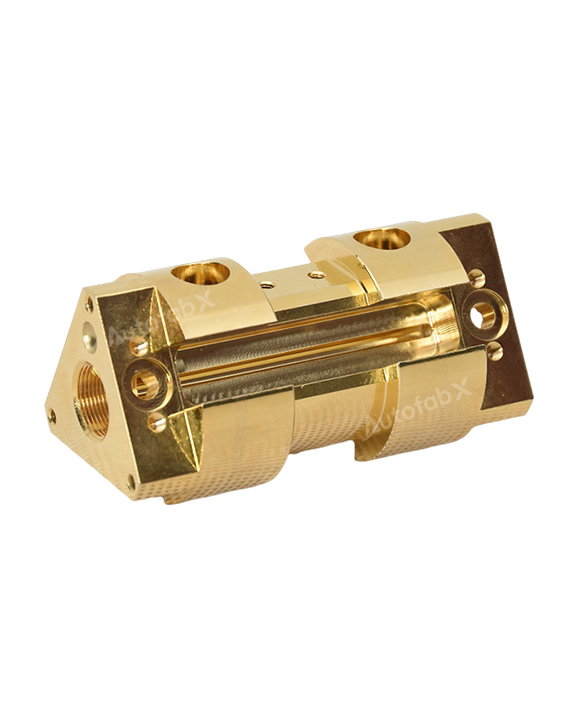
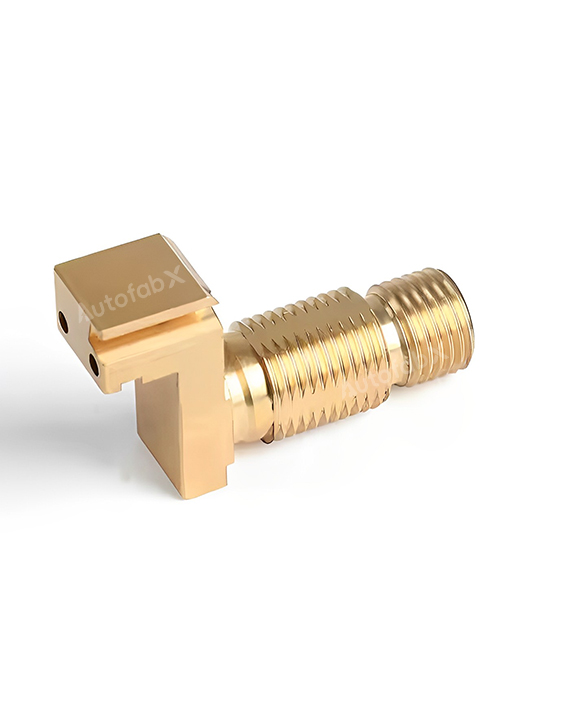
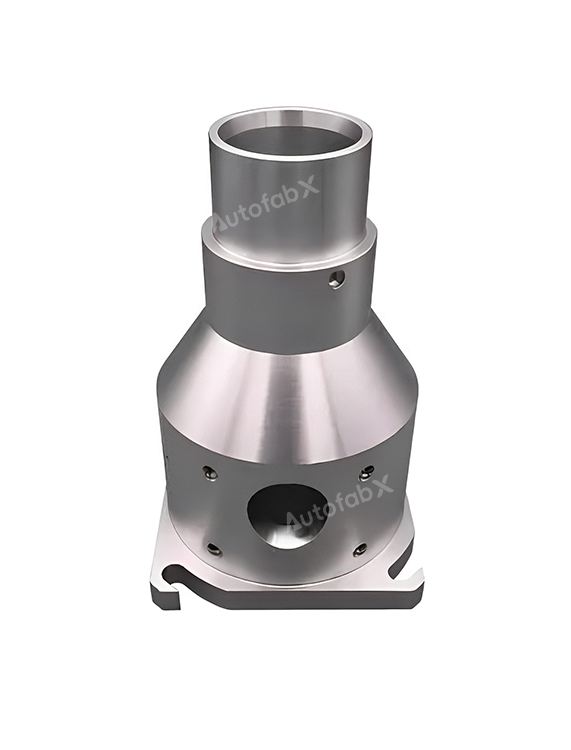
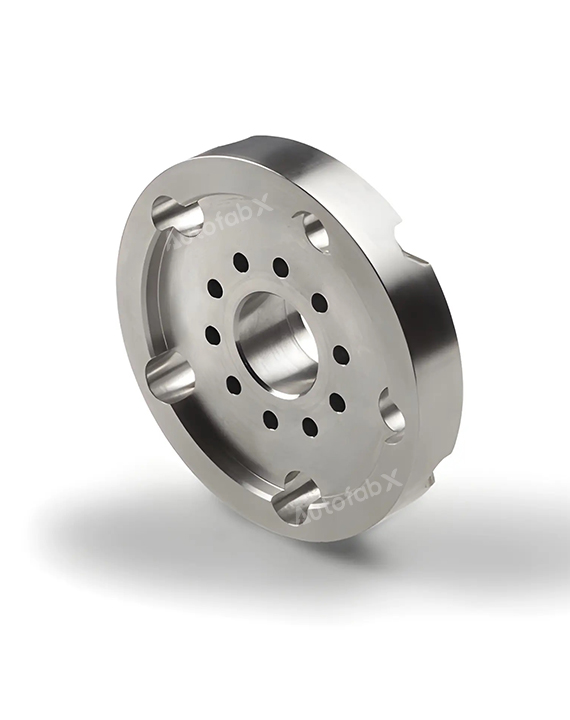
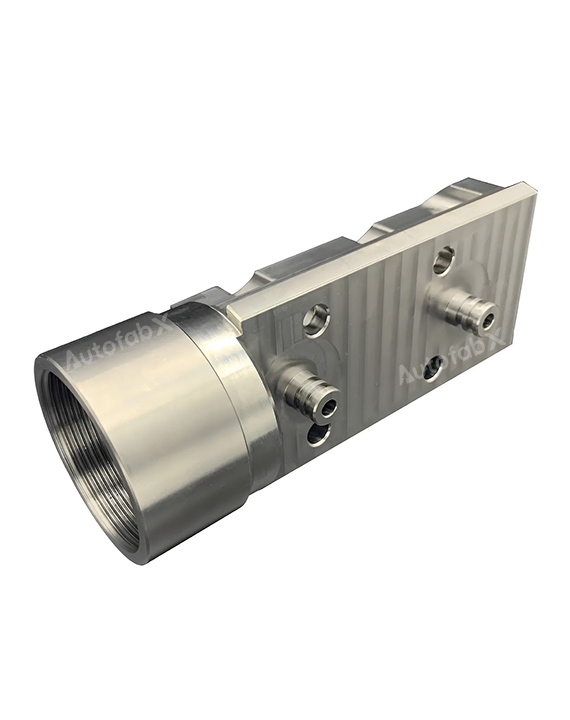
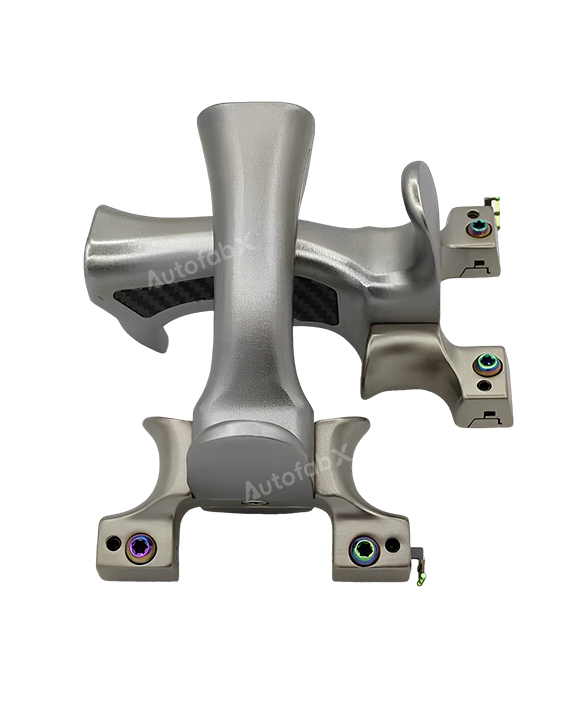

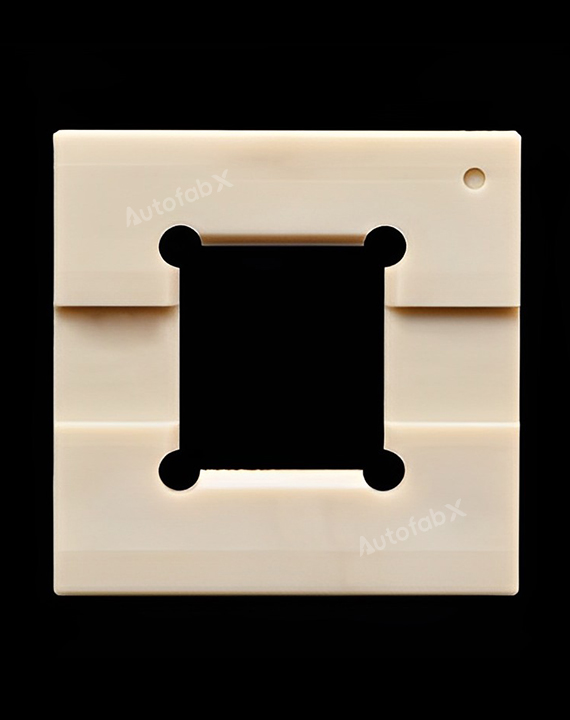
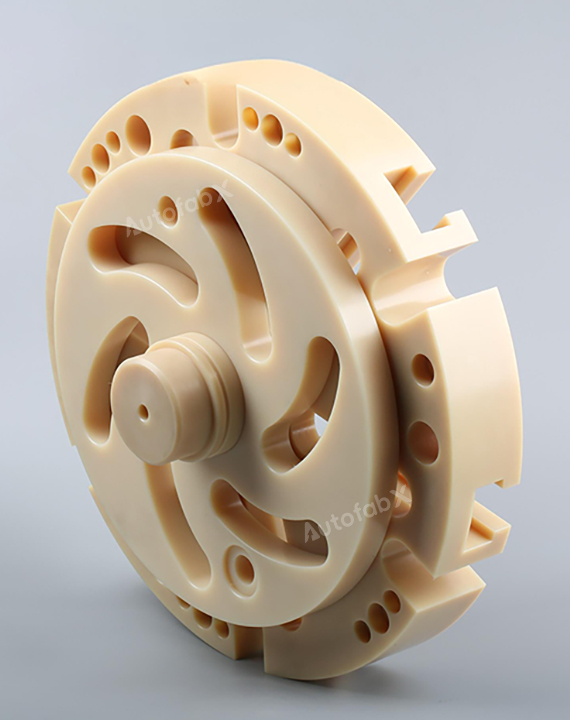
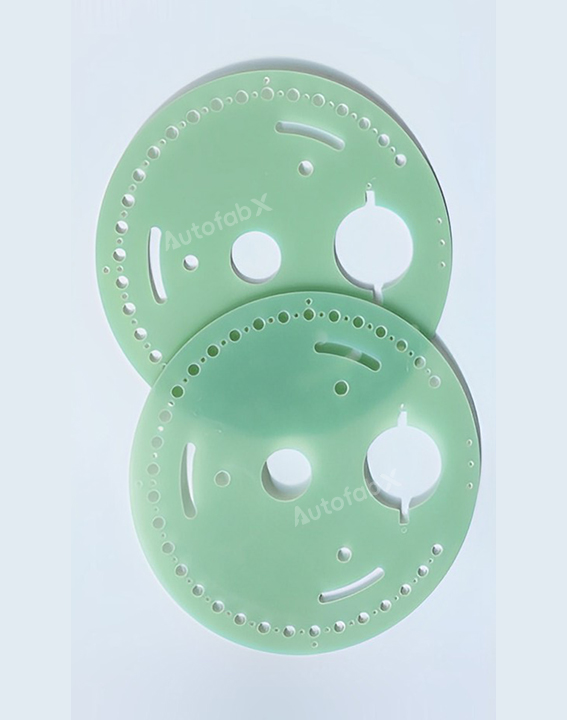
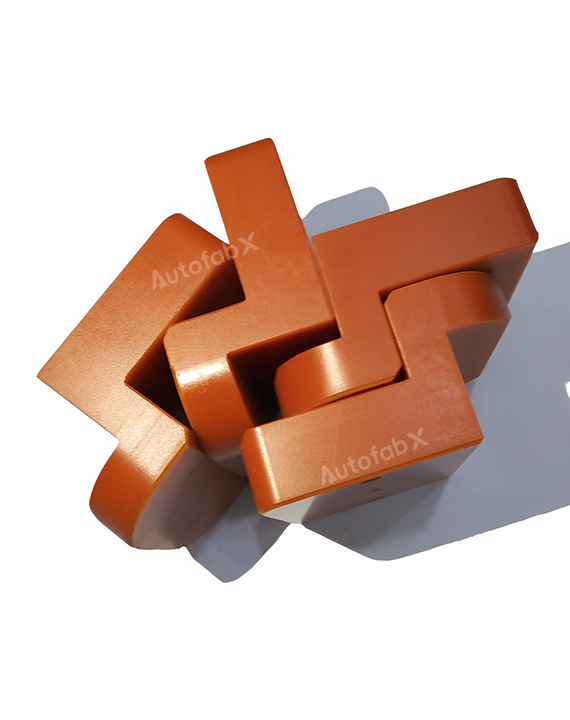
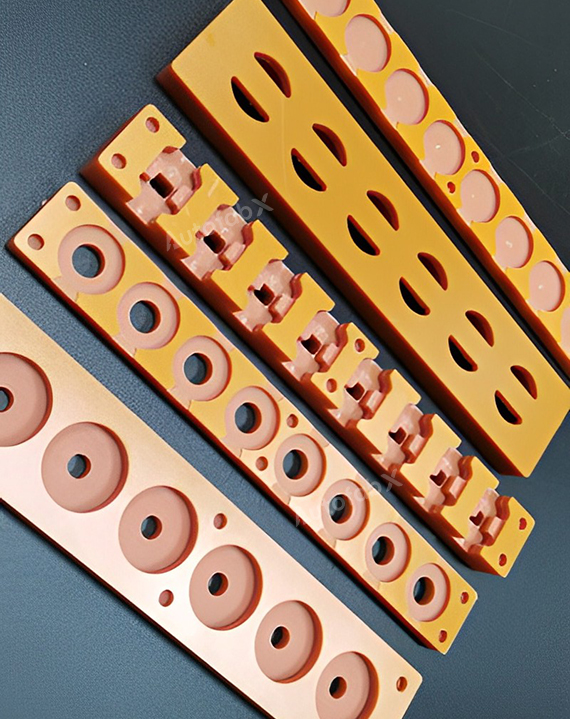
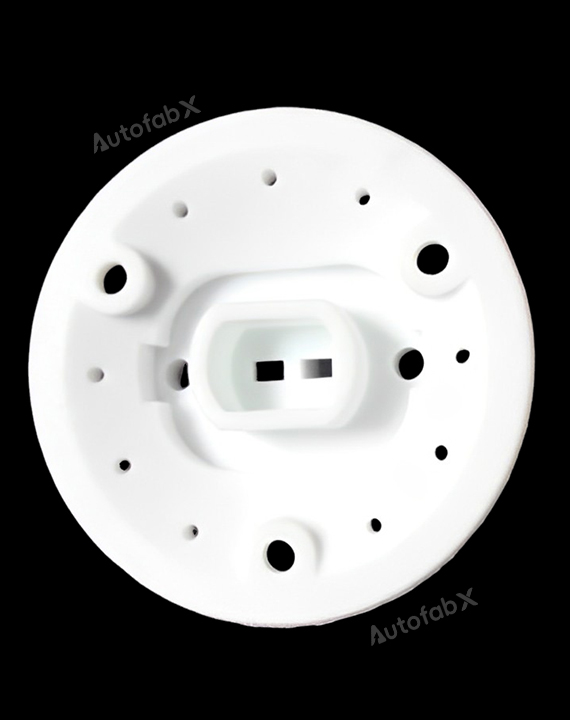
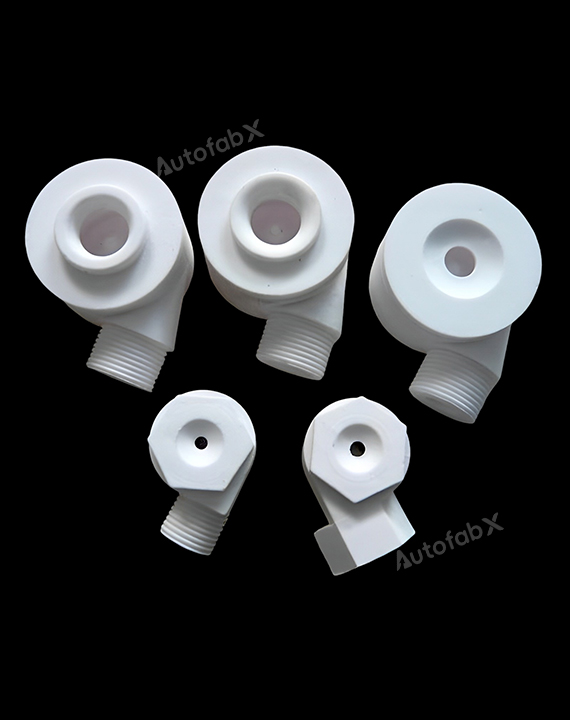
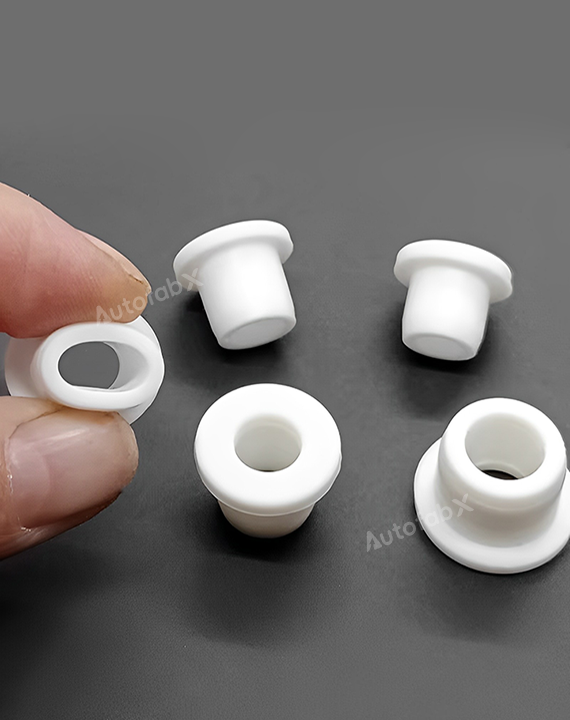
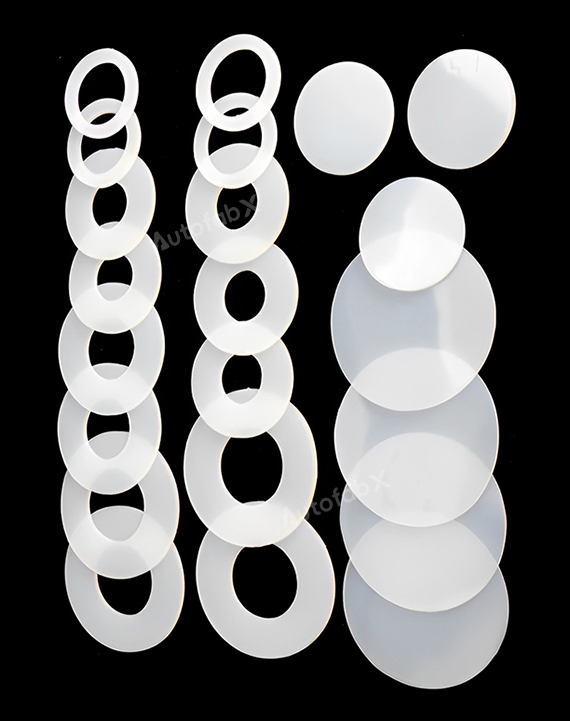